DRYCAKE DR Decanter Centrifuge
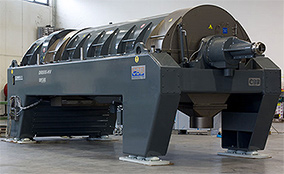
Langley Separation and Process offers the complete range of DRYCAKE DR Model horizontal decanter centrifuges incorporating decades of mechanical knowledge and process experience to provide an effective, low-maintenance solution for continuous liquid-solids separation, liquid clarifying and/or solids dewatering with advanced mechanical features and superior processing performance.
The DRYCAKE DR Decanter Centrifuges are available in a variety of configurations with capacities from 20-gpm to 800-gpm including two phase (liquid/solid) and three phase separation (liquid/liquid/solid) designs. This makes the range of DRYCAKE DR Decanter Centrifuges very versatile and capable of adapting to a wide range of industrial and municipal applications. The automated controls also make these machines easy to adjust over a wider range of process conditions and require little operator attention to maintain process parameters. Our centrifuges are designed for high performance and reliable operation under the most strenuous of conditions.
Model | Motor & Hydraulic Back-drive | Bowl Dia. | Max “G” | Flow rate |
---|---|---|---|---|
DR300H | 15-HP 240/480/3/60 | 11″ | 3,800 “G” | up to 40-gpm |
DR400H | 25-HP 240/480/3/60 | 15″ | 3,500 “G” | up to 80-gpm |
DR450H | 40-HP 240/480/3/60 | 17″ | 3,000 “G” | up to 150-gpm |
DR500H | 60-HP 240/480/3/60 | 20″ | 3,000 “G” | up to 200-gpm |
DR650H | 100-HP 240/480/3/60 | 26″ | 3,000 “G” | up to 350-gpm |
DR800 | 175-HP 240/480/3/60 | 31″ | 3,000 “G” | up to 500-gpm |
Standard available automation package feature back-drive controls plus PLC with color HMI and VFD motor controls. Custom automation and programming of additional process controls is available. Complete custom skid packages with common structural steel skid with pumps, sludge conveyor, hydraulic unit, and control panel with all components pre-mounted, wired, and piped for turnkey operation and portability are also available.
15 Reasons to Choose a DRYCAKE DR Decanter Centrifuge:
Available in 2-Phase and 3-Phase design configurations for separation of liquid/solids or liquid/liquid/solids
The dedicated electronic DPC (Decanter Process Controller) automatically manages the process cycle and safely controls the machine while maximizing the process potential of the DR Decanter
Replaceable solid discharge erosion resistant wear bushings are easily accessible given the unique rotating assembly cover design simplifying maintenance and reducing downtime
Adjustable Liquid discharge level plates are easily accessible and adjusted due to the unique rotating assembly cover design simplifying maintenance and reducing downtime
A unique sludge discharge cover scraper assembly prevents sludge from accumulating on the inside of the cover and blocking the solid discharge of the machine
Hydraulic and electric scroll back-drive transmission group options including an energy recovery system during machine operation which reduces the energy consumption of the DR Decanter
Scroll features a sludge baffle disc which increases the working capacity of the DR Decanter and improves separation performance
Four (4) piece machine rotating assembly covers with hydraulic actuators simplifies the operator’s job making inspecting and maintaining the specific sections of the rotating assembly easy and convenient
Rotating assembly group is easily extracted from above the machine simplifying maintenance and reducing removal time
Head-walls and bowl sections made from high strength forgings and centrifugal castings to improve resistance and homogeneity of bowl structure
Scroll features solid stainless steel fabrication to improve resistance, stiffness and longevity
Heavy-duty DR Decanter base frame fabrication dampens vibrations and minimizes vibration transmission to the machine mounting structure
Twenty (20) years of design and manufacturing experience in sludge separation processes assures customer satisfaction and meeting specific process and facility requirements
Optional remote monitoring and operational assistance reduces waiting time for resolution of possible problems
Technical service follow-up within 24 hours (in Italy or 48 hours abroad) when possible issues occur DRYCAKE provides a Toll Free: 1-877-379-2253 technical support and resolution
Characteristics of Two-phase Separation
DRYCAKE DR Decanter Centrifuges allow separation between liquid and solid phases contained within a feed-slurry of industrial or municipal wastewater sludges or other industrial and/or food applications.

Inlet sludge, through feed pipe, will be conducted inside the bowl of the decanter and here separation of liquid phase from solid one will happen thanks to the action of centrifugal force. Liquid phase will be expelled from bowl front part thanks to specific level plates than can be adjusted on outlet diameter, while solid phase will be convoyed from the screw to exit openings on bowl rear part, where it will be then expelled. The feed slurry is introduced through an inlet feed tube into the scroll feed zone where it is accelerated and directed into the spinning bowl of the decanter centrifuge. The solids which have a higher specific gravity than the liquid phase will rapidly settle out on the inner wall of the centrifuge bowl due to the intense acceleration of centrifugal force over 3,000 x “gravity” leaving a clear inner ring liquid phase. The liquid phase flows in a helical channel between the scroll flights moving toward the large diameter end of the centrifuge bowl where the clarified liquid is expelled at a depth controlled by the adjustable liquid level discharge plates on the outlet diameter of the liquid end head-wall. The liquid phase or “centrate” then overflows into the liquid discharge cover and gravity drain from the machine. The compacted solid phase is discharged from the decanter centrifuge bowl by scroll which rotates at slightly different speed (differential speed) as controlled by the back-drive conveying the solids up the conical bowl section to the discharge ports. The dry solids are discharged into the solids discharge cover where a solids scrapper keeps the cover clear of solids cake build-up.
Characteristics of Three-phase Separation
DRYCAKE DR Decanter Centrifuges allow separation between heavy liquid phase / light liquid phase and solid phases contained within a feed-slurry of industrial or municipal wastewater sludges or other industrial and/or food applications.The feed slurry is introduced through an inlet feed tube into the scroll feed zone where it is accelerated and directed into the spinning bowl of the decanter centrifuge. The solids which have a higher specific gravity than the liquid phase will rapidly settle out on the inner wall of the centrifuge bowl due to the intense acceleration of centrifugal force over 3,000 x “gravity” leaving a clear inner ring liquid phase. The liquid phase flows in a helical channel between the scroll flights moving toward the large diameter end of the centrifuge bowl where the clarified heavy liquid phase is expelled at a depth controlled by the adjustable liquid level discharge plates on the outlet diameter of the liquid end head-wall. The Light liquid phase is expelled separately from bowl through adjustable depth nozzles. Both liquid “centrate” phases then overflows into their respective liquid discharge covers and gravity drain from the machine. The compacted solid phase is discharged from the decanter centrifuge bowl by scroll which rotates at slightly different speed (differential speed) as controlled by the back-drive conveying the solids up the conical bowl section to the discharge ports. The dry solids are discharged into the solids discharge cover where a solids scrapper keeps the cover clear of solids cake build-up.
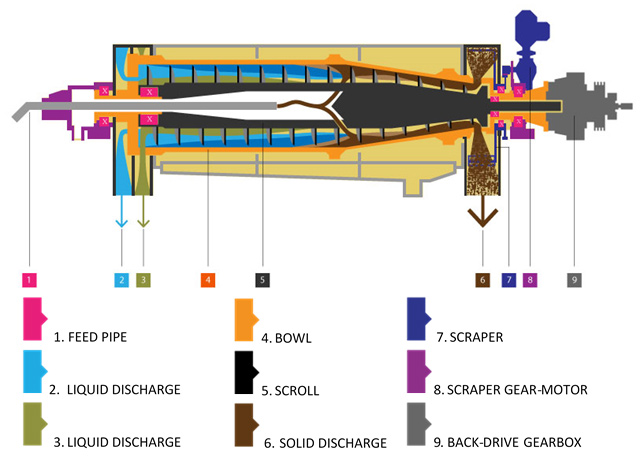

DR Decanter Centrifuge Machine Components / Scroll Back-drive Transmission Options
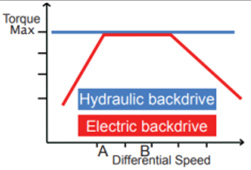
Having the ability to adjust the scroll differential speed and maintain consistent back-drive torque control is essential to optimal performance. In centrifuge operation, the torque on the scroll back-drive expresses the pressure applied to squeeze the liquid phase out of the solid phase. Too much scroll back-drive torque and the liquid will come rushing out the solids discharge, not enough and you won’t get a DRYCAKE. Hydraulic back-drives are typically preferred over electric back-drives because they offer better torque control and a flat performance curve per the graph. However DRYCAKE offers the DR range of decanter centrifuges with a selection of different back-drive transmission types to meet specific customer and / or application requirements.
Available Back-drive transmission types
Variable speed scroll back-drive with electric drive motor and closed circuit hydraulic pump/motor

Variable speed scroll back-drive with double electric drive motors
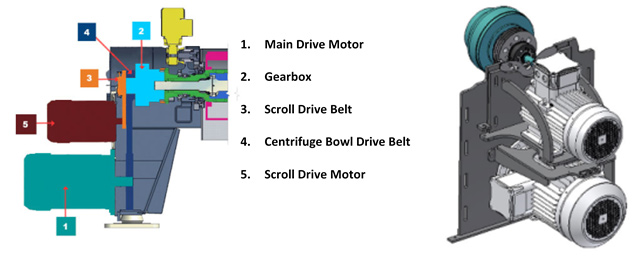
Fixed speed back-drive with electric drive motor
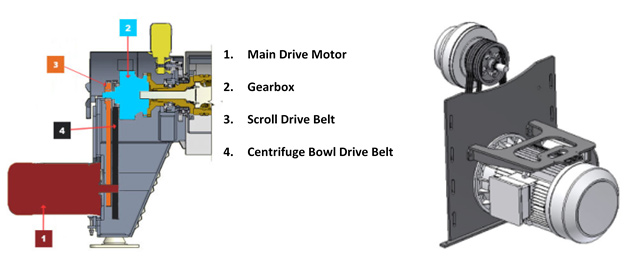
Decanter Centrifuge Bowl and Scroll Assemblies

Adjustable Liquid Level Weir Plates
All other major manufacturers make use of several different bothersome weir plates to change liquid levels. These are usually half-crest moons that are difficult to change and are often lost in storage. DRYCAKE only makes use of one plate. So, when the liquid levels do need changing the plate is exactly where you need it, on the machine. Changing the liquid levels is also easier on the DRYCAKE because of the three section hinged cover, which provided quick and easy access to the weir plate.
Replaceable Sludge Discharge Wear Bushings
The discharge bushings are very easy to replace due to our three section hinged cover and the use of standard tools. We can also rotate our discharge bushings to get more life out of them. The wear on the bushings is always on the same side, so simply rotate the bushing in place 1/4 turn to gain up to 4 times more wear life.
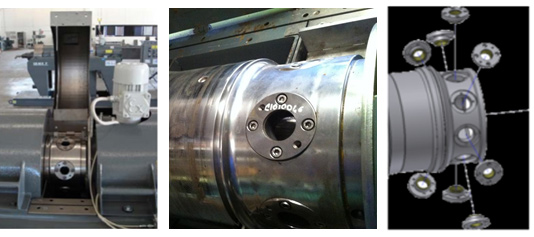
Integrated zero-footprint hydraulic back drive and Reservoir System
One of the biggest concerns we get from operators in regards to hydraulic back drives is the location and connection of the hydraulic tank. Typically a hydraulic unit is placed next to the centrifuges with the hydraulic lines running on the ground to the centrifuge. DRYCAKE has addressed this issue by simply using the legs of the centrifuge as hydraulic tank. This reduces the footprint of the complete supply, and removes any, potentially unsafe, connection lines lying around. In effect DRYCAKE offers.
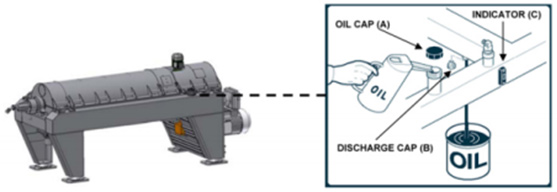
Decanter Centrifuge Machine Base Frame and Cover Assemblies
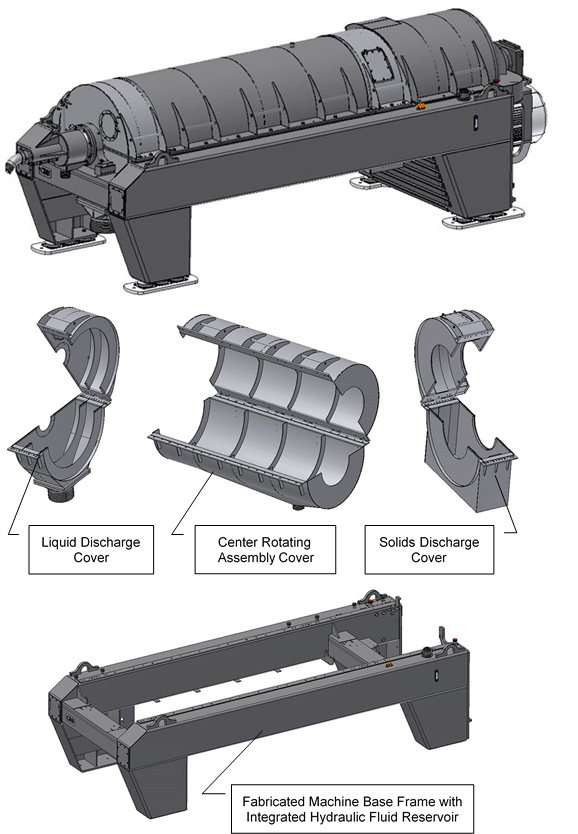
Sludge Cover Scraper Mechanism
Solids build up in the sediment sludge discharge cover is one of the major reasons that a centrifuge stalls. The DRYCAKE centrifuges are equipped with a separate internal cover scraper and continuous full geared, independently driven low-speed (5RPM) solids scraper to prevent this from happening. The solids cake discharge of a centrifuge is thrown against the internal walls of the sediment sludge discharge cover with a force over 1000xG. Normally, the sediment falls down because of gravity, but with alum sludge and other sticky sludges, the sediment build ups clogging the centrifuge solids discharge.
If the discharge is clogged, no solids can leave the centrifuge, and the bowl of the centrifuge will fill up completely, causing the centrifuge to fault and shut down. It is then necessary to remove the scroll and clean out the bowl. In certain applications, this might require a 30 ton winch to extract the scroll from the bowl. Some other manufacturers also have a scraper but it runs with the bowl/scroll assembly, which results in excessive wear in the scraper blades and can cause increase in loss of balance. Others may use a chain driven scraper motor resulting in sealing problems in the discharge chamber. The DRYCAKE Scraper is fully geared, uses ball bearings, and operates independently from the bowl and the scroll. This feature sets the scraper of the DRYCAKE centrifuge apart from every other major manufacturer.
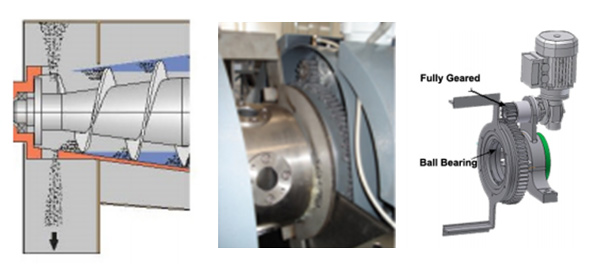
Why Purchase a DRYCAKE DR Decanter Centrifuge?
The centrifuge is highly automated. After startup, which is automated, the operator can walk away. Usually, an operator is only required to periodically check on the operation of the system to insure proper continued operation.
The shutdown sequence of the centrifuge is also completely automated – just push a button. The belt press will usually require one half hour of wash down, which is time consuming and messy.
The belt press takes up more space – the centrifuge takes up considerably less space.
The centrifuge is totally enclosed. This eliminates odor and mess in the plant.
Operators can be exposed to aerosols in the air due to high pressure wash of the belt. This does not occur with a centrifuge.
The belt press uses a continuous flow of wash-water, which adds loading to the plant. The centrifuge does not.
The centrifuge will normally provide a cake with 2% or higher cake solids than a belt press. The actual difference will depend upon the design and quality of the belt press. A lower cost belt press will produce even lower solids. This adds to hauling and disposal cost. Over 5 or 10 years, this difference can easily pay for the centrifuge.
A belt press is lower in initial cost than a centrifuge. However, when installation costs are included, system cost will tend to equalize.
The price for ancillary equipment such as feed pump, polymer system, conveyors, etc. will be the same for a belt press or a centrifuge. Therefore, when the entire system, including installation, is considered, the cost differential is minimal.
A belt press requires a special foundation. The floor under the press must be sloped to a drain with curbing all around. This adds to the installation cost.
Why buy a skid mounted or containerized DRYCAKE DR Decanter Centrifuge system? A skid mounted or containerized DRYCAKE DR Decanter Centrifuge system offers additional advantages:
- The skid mounted system has a very low installation cost since the entire equipment package is delivered completely pre-mounted, pre-piped and pre-wired
- A skid mounted or containerized DRYCAKE DR Decanter Centrifuge system does not require a special foundation – only requires a flat floor.
- All components are tested in the factory before shipment to insure proper operation. This greatly reduces startup time and cost.
Mobile Systems and Complete Customized Decanter Centrifuge Systems
Langley Separation and Process can deliver complete skid mounted turnkey decanter centrifuge systems featuring custom automation / control panel, pumps, discharge chutes, pipe work, feed / receiving tanks, polymer systems, skid packages, platforms, and other accessories and options. All DRYCAKE equipment is customizable to project specifications and can be provided with the following Explosion proof electrical options: Class 1 Div 1 and/or Class 1 Div 2.
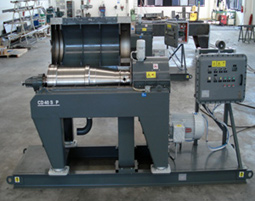
In addition to our stationary decanter centrifuge systems, we offer mobile dewatering solutions for municipal and industrial applications for up to 400-gpm. These containerized systems include polymer make-up systems, feed pumps, flow-meters, cake discharge conveyors, piping, and integrated control panel. Container options include lighting, heating, windows, doors and stairs.
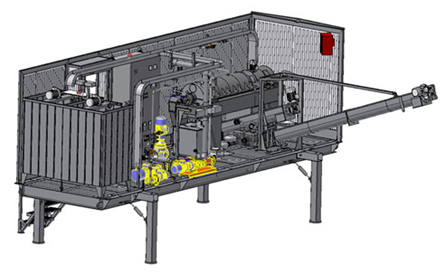
DRYCAKE also offers powder, emulsion, and combination powder/emulsion polymer make-up systems for continuous automatic operations.
DRYCAKE also offers Shaft-less Screw conveyors • Belt conveyors • Slewing conveyors • Horizontal bi-directional distribution conveyors • Vertical conveyors • Live bottom conveyors • Cake pumps.
Shaft-less screw conveyors are commonly used for conveying dewatered cake discharge. The cake is then discharged directly into another conveyor, a discharge bin, distribution or slewing conveyor. Our cake pumps are a good alternative to conveying systems, when dealing with large volumes in small space and distance.
DRYCAKE Decanter Centrifuge Applications
Case Studies
Frequently Asked Questions
- Dewatering Equipment Fundamentals (630K, PDF)