DAF Sludge Dewatering
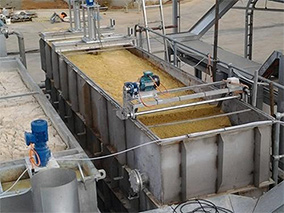
Dissolved air flotation or DAF sludge dewatering and filtering systems are used in a variety of industries and applications to remove suspended solids, fats, oils and greases from a variety of wastewaters. DAF systems work by injecting dissolved air (bubbles) into a waste stream typically with the addition of coagulants and flocculants which attach to solids so they will float to the surface, where the floating solids cake is skimmed off. While DAF systems are used effectively in many applications, the associated mess and disposal costs required to handle the solids skimmed off of the fluid can be significant. As a proven leader in sludge dewatering Langley Separation and Process specializes in solving problems through application engineering and DRYCAKE DR Decanter Centrifuges can help with most all types of DAF sludge dewatering.
DRYCAKE DR Decanter Centrifuges are an effective and proven piece of equipment for dewatering the solids skimmed off most DAF wastewater systems, which are typically wet, sloppy, and expensive to handle. Centrifuges can often outperform conventional belt filter presses given the gelatinous nature of many DAF skimmings. With disposal issues and costs increasing the centrifuge provides many cost saving advantages:
- Reduces total disposal volume by as much as 70%
- Produces stackable cake like sludge
- Reduces handling costs
- Increases options for sludge disposal

DRYCAKE DR Decanter Centrifuges offer a wide range of available sizes and configurations of decanter centrifuges and process options and can help you realize the above benefits. Please call or e-mail Langley Separation and Process and provide one of our application specialists with the following basic information and we will give you a quick assessment of how it can work for you.
- How much DAF sludge volume does your plant produce?
- What does it cost to dispose of your DAF Sludge?
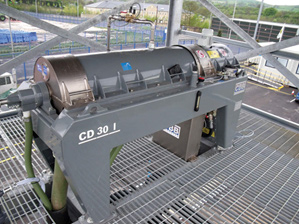
Basic DAF Sludge Decanter Centrifuge Dewatering System Diagram

Basic Process Description
Process wastewater flows into the DAF tank and suspended solids float to the surface forming a layer or blanket of material, which is periodically or continuously scraped off and into a holding tank and / or mix tank.
The mix tank gently agitates the solids into a homogeneous dilution of solids and liquid, which is then fed to the centrifuge using a progressive cavity feed pump.
If necessary an additional chemical additive may be introduced to help facilitate a more separable and dryer sludge cake. This is more prevalent with “fatty” solids.
A progressive cavity feed pump pulling from the bottom of the mix tank continuously feeds to the centrifuge and is controlled by a VFD to adjust pump speed and flow rate. The centrifuge returns the centrifugally clarified liquid back to the head of the DAF or collection pit / tank. The centrifuge will periodically stop and discharge the separated solids into a sludge hopper placed below the centrifuge.
A float switch opens a normally closed butterfly valve in the clarified liquid discharge line and adds re-circulated make-up water to the mix tank during low level conditions
DRYCAKE DR Decanter Centrifuges offer numerous advantages on DAF sludge dewatering applications:
- Centrifuges require a small amount of floor space relative to their capacity
- Centrifuges require minimal operator attention
- Easy to use and adjust with no full time operator required for continuous operation
- Operators have low exposure to pathogens, aerosols, hydrogen sulfide or other odors
- Centrifuges can handle higher than design loadings and the percent solids recovery can usually be maintained with the addition of a higher polymer dosage
- DAF systems utilizing chemical polymers or flocculants can provide excellent water treatment results and relatively dry sludge cake when incorporating centrifuge technology to dewater the DAF sludge
- Decanter centrifuge offers maximum flexibility and adjustability to meet process requirements for solids capture and dewatering solids discharge with simple adjustments
- Wide range of slurry feed rates, feed solids concentrations and feed materials can be processed with coarse prescreening recommended to remove large and other miscellaneous debris
- No filter media to blind-off
- No screens or filter cloths to replace
- Centrifuges are easier to clean
- All stainless steel product contact surfaces make the machines resistant to corrosion
- Major maintenance items can be easily removed and replaced
- Full scale pilot size machines available for testing and all pilot test data can be directly scaled to production feed rates

Mobile onsite application test units
LS&P and DRYCAKE maintain a full scale mobile decanter centrifuge test trailer for onsite application testing and centrifuge pilot testing. Portable systems feature a production model centrifuge mounted in a trailer with all the system controls and ancillary equipment such as pumps, polymer systems, and sludge auger as well as connection hoses for a complete set-up.
A typical one-week test program is specifically designed to evaluate performance, provide operational data, and determine optimal centrifuge capacity on representative material as well develop treatment experience with the centrifuge process. The test program will typically consist of a series of predetermined test runs designed to evaluate the cause-effect relationship between certain key performance parameters:
- Throughput vs. cake solids
- Throughput vs. solids capture rate
- Polymer addition /selection and effect on cake solids / solids capture rate
Langley Separation and Process can deliver complete skid mounted turnkey decanter centrifuge systems featuring custom automation / control panel, pumps, discharge chutes, pipe work, feed / receiving tanks, polymer systems, skid packages, platforms, and other accessories and options.
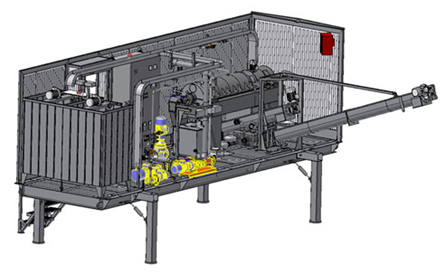
All DRYCAKE equipment is customizable to project specifications and can be provided with the following Explosion proof electrical options: Class 1 Div 1 and/or Class 1 Div 2.
In addition to our stationary decanter centrifuge systems, we offer mobile dewatering solutions for municipal and industrial applications for up to 400-gpm. These containerized systems include polymer make-up systems, feed pumps, flow-meters, cake discharge conveyors, piping, and integrated control panel. Container options include lighting, heating, windows, doors and stairs.
DRYCAKE also offers powder, emulsion, and combination powder/emulsion polymer make-up systems for continuous automatic operations.
DRYCAKE also offers Shaft-less Screw conveyors • Belt conveyors • Slewing conveyors • Horizontal bi-directional distribution conveyors • Vertical conveyors • Live bottom conveyors • Cake pumps