Biosolids
Municipal and industrial wastewater treatment plants are designed to produce a clean, safe water discharge within the required discharge limits. Centrifugal thickening and dewatering of sewage sludge and biosolids is a process that uses the power of centrifugal force to separate wastewater solids from liquid. Thickening before digestion or dewatering reduces the tankage needed for digestion and storage by removing water. Dewatering removes more water and produces a drier material referred to as “cake”. Centrifuges have been used in wastewater treatment since the 1930s. New plants built today are becoming more and more sophisticated and decanter centrifuges are extensively used for liquid / solid separation, sludge dewatering and sludge thickening applications. The complexity of the plant will depend on the immediate environmental considerations and the consent limits negotiated with the authorities.
There are basically (2) two decanter centrifuge applications found in most municipal and industrial wastewater treatment facilities and the wastewater treatment industry in general:
Feeding the decanter centrifuge a liquid slurry (around 1–3% DWS) and thickening it to approximately 8% DWS, often prior to feeding the thickened material to a biological digester.
Feeding the decanter centrifuge with similar slurry and dewatering the solids to a relatively dry stackable cake of leach free solids prior to transportation for disposal. In the second example the solids typically come from the primary clarifier or secondary clarifier after biological treatment.
A simplified and typical flow-chart for wastewater applications is shown below although not all process steps are present, particularly for industrial wastewater.

The DRYCAKE DR range of decanter centrifuges is ideally designed for these applications. Controlling the decanter centrifuge operating parameters optimizes the consistency of the discharged sludge cake and can be regulated to suit the disposal requirements. Slurry for land application should be thickened to reduce the volume of water but still needs to be fluid enough to be easily spread or evenly pumped for land application. Digester feed slurry can often be thicker but typically requires a pump-able sludge. When the discharged sludge will be disposed of via landfill, dewatering the feed slurry to a stackable consistency reduces weight, volume and disposal costs.
Thickening of Activated Sludge
Many effluent treatment plants use a biological treatment process to reduce the wastewater COD and BOD before discharging into the downstream environment. During the treatment process colonies of bacteria develop and grow forming a biological body producing a solid waste as it feeds on the chemicals and nutrients.

It is necessary to continuously purge the growing biological mass to control its activity and efficiency. The purge feed stream is usually in the form of dilute slurry ranging from 0.5% to 3% DWS, which is easier to handle when first thickened. Some of the thickened slurry can be returned to the biomass to maintain an optimum concentration of bacteria while the remaining waste activated sludge is processed for disposal.
A basic decanter centrifuge installation provides the flexibility to easily “adjust” operating parameters “on-the-fly” and produce the desired choice of thickened sludge concentrations. A typical installation allows for the use of a polymer to aid separation but polymer is not necessarily essential. The decanter centrifuge will thicken an activated sludge without polymer producing an ideal 6%-DWS solids output for land spraying applications. However, the liquid centrate will often remain cloudy in the range of 0.2%-DWS, which can still pose a disposal problem. Many industrial and municipal waste treatment facilities will then often use a low concentration of polymer to clear up the centrate to less than 200-ppm DWS.
The parameters most often used to produce thickened digester feed slurry include increasing the polymer concentration and adjusting the bowl and conveyor speed of the decanter centrifuge, which will typically produce a clear centrate and solids discharged at 8%-DWS. Once the system is optimized, the DRYCAKE scroll drive system will automatically adjust its speed to control the consistency of the discharged solids cake.

A further increase of the polymer concentration and adjustment of the decanter centrifuge operating parameters will thicken the feed slurry and yield a stackable solids cake of approximately 12%-DWS. And once the operating conditions are optimized, the decanter centrifuge will control the solids discharge with the automatic adjustment of the differential scroll speed. The decanter can both thicken and dewater, switching between the two process applications in a matter of minutes without interruption of the feed slurry.
It is not possible to state cake dryness figures given the process variations that exist from waste treatment plant to plant but the decanter centrifuge will usually produce a cake that is touch dry and sometimes friable. Slurries from a primary clarifier will typically range from 28 to 36%-DWS. And while waste activated sludges can also appear friable they are typically only 15 to 22%-DWS. Even though moisture concentration can vary widely, consistent solids will be discharged from the decanter centrifuge by optimizing the system operating parameters.
Dewatering Activated Sludge
In all thickening and dewatering applications when a polymer is used to aid separation the centrate clarity will typically look like the photograph with less than 200-ppm DWS.
Note: The decanter centrifuge will often produce better results than other dewatering equipment when secondary or biological sludges are present in the material to be processed. The primary reason for this is decanter centrifuges do not use filter media for separation and dewatering, which can often become blocked or blinded by biological sludges.
Thickening and Dewatering Digested Sludge
As with activated sludge, decanter centrifuge operating parameters can be adjusted to thicken or dewater digested sludge. Typical performance for dewatered digested sludge:
Inlet solids | 2 to 4%-DWS |
Outlet solids | 28 to 33%-DWS |
Polymer required | 9 to 14-lbs/1000lbs-DWS |
Solids recovery | > 97% |
Centrate quality | < 200-ppm |
Fully dewatering digested sludge is not always necessary unless the objective is to reduce the total volume for minimizing transport and landfill costs. Some industrial and municipal wastewater treatment facilities choose only to thicken the sludge to meet their specific handling requirements.
Decanter Centrifuge Results Summary Chart | ||||
---|---|---|---|---|
Thickening and Dewatering an Activated Sludge at 1% to 2%-DWS | ||||
Discharged Solids | Centrate | Polymer | ||
Feel | Concentrate | Turbidity | Concentrate | Lbs / 1,000lb-DWS |
Runny | 6% DWS | Cloudy | 0.2% | 0 |
Pumpable | 8% DWS | Clear | <200-ppm | 1–1.5 |
Stackable | 12% DWS | Clear | <200-ppm | 4–5 |
Friable | 18% DWS | Clear | <200-ppm | 10–12 |
For each site, it is important to optimize the use of polymer to be cost effective and still reach an acceptable goal for solids dryness.
(For example a plant thickening 800,000 gallons per day of activated feed slurry at 1%-DWS up to 8% pump-able slurry with a clear centrate, would require approximately 66 to 100-lbs per day of polymer).
DRYCAKE DR Decanter Centrifuge units are supplied with advanced controls for both variable speed bowl and scroll back-drive optimization making them easily configured to produce a wide range of results. To produce wetter solids, speed up the conveyor drive and turn down the polymer feed rate to between 1 to 2-lbs/1,000-lbs DWS. To produce a thicker solids consistency, slow down the conveyor drive and increase the polymer feed rate again. At 3 to 4-lbs/1000-lbs DWS, thickened solids @ approximately 12%-DWS will feature a consistency with slightly visible free water but as the rate of polymer is increased, the solids become more homogenous and for example @ approximately 18%-ds the solids can be handled satisfactorily with a mechanical shovel. By increasing the use of polymer dosage and controlling the decanter operating parameters, the discharged solids become progressively drier.
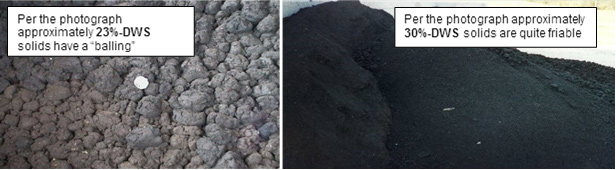
DRYCAKE DR Decanter Centrifuges offer numerous advantages on Biosolids applications:
Centrifuges may offer lower overall operation and maintenance costs and can often outperform conventional belt filter presses
Centrifuges require a small amount of floor space relative to their capacity
Centrifuges require minimal operator attention
Easy to use and adjust with no full time operator required for continuous operation
Operators have low exposure to pathogens, aerosols, hydrogen sulfide or other odors
Centrifuges can handle higher than design loadings and the percent solids recovery can usually be maintained with the addition of a higher polymer dosage
DAF systems utilizing chemical polymers or flocculants can provide excellent water treatment results and relatively dry sludge cake when incorporating centrifuge technology to dewater the DAF sludge
Decanter centrifuge offers maximum flexibility and adjustability to meet process requirements for solids capture and dewatering solids discharge with simple adjustments
Wide range of slurry feed rates, feed solids concentrations and feed materials can be processed with coarse prescreening recommended to remove large and other miscellaneous debris
No filter media to blind-off
No screens or filter cloths to replace
Centrifuges are easier to clean
All stainless steel product contact surfaces make the machines resistant to corrosion
Major maintenance items can be easily removed and replaced
Full scale pilot size machines available for testing and all pilot test data can be directly scaled to production feed rates

Mobile onsite application test units
LS&P and DRYCAKE maintain a full scale mobile decanter centrifuge test trailer for onsite application testing and centrifuge pilot testing. Portable systems feature a production model centrifuge mounted in a trailer with all the system controls and ancillary equipment such as pumps, polymer systems, and sludge auger as well as connection hoses for a complete set-up.
A typical one-week test program is specifically designed to evaluate performance, provide operational data, and determine optimal centrifuge capacity on representative material as well develop treatment experience with the centrifuge process. The test program will typically consist of a series of predetermined test runs designed to evaluate the cause-effect relationship between certain key performance parameters:
- Throughput vs. cake solids
- Throughput vs. solids capture rate
- Polymer addition /selection and effect on cake solids / solids capture rate
Langley Separation and Process can deliver complete skid mounted turnkey decanter centrifuge systems featuring custom automation / control panel, pumps, discharge chutes, pipe work, feed / receiving tanks, polymer systems, skid packages, platforms, and other accessories and options.
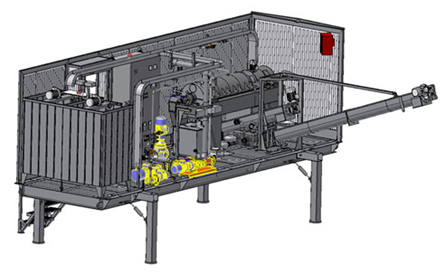
All DRYCAKE equipment is customizable to project specifications and can be provided with the following Explosion proof electrical options: Class 1 Div 1 and/or Class 1 Div 2.
In addition to our stationary decanter centrifuge systems, we offer mobile dewatering solutions for municipal and industrial applications for up to 400-gpm. These containerized systems include polymer make-up systems, feed pumps, flow-meters, cake discharge conveyors, piping, and integrated control panel. Container options include lighting, heating, windows, doors and stairs.
DRYCAKE also offers powder, emulsion, and combination powder/emulsion polymer make-up systems for continuous automatic operations.
DRYCAKE also offers Shaft-less Screw conveyors • Belt conveyors • Slewing conveyors • Horizontal bi-directional distribution conveyors • Vertical conveyors • Live bottom conveyors • Cake pumps