Potato Processing
DRYCAKE DR Decanter Centrifuges are commonly installed at potato and root crop processing plants of potato chip and french-fry producers as well as flake and potato packers and applications typically fit into four (4) groups:
- Starch Dewatering
- Wastewater Effluent Treatment
- Potato Meal
- Wash Water Recycling / Cleaning (mud dewatering)
Starch Dewatering
With many installations in the starch recovery application and excellent co-operation with our clients, we have extracted considerable data from on-site processing results. The majority of the centrifuges installed for starch recovery are operated as lower “G” reduced speed type decanters since these machines can operate at less than 2,000 x “G” and produce the desired results. Hydro-cyclones and other systems are commonly used for starch recovery but these generally produce a wetter and more unmanageable starch when compared to a decanter centrifuge. Plus these systems typically do not recover the starch with the same separation efficiently as the decanter centrifuge. Units installed to recover wash water starch from cutting and / or slicing potatoes at a potato chip manufacturer would on average produced approximately 2-3 tons of recoverable starch from every 100 tons of potatoes processed. The separated starch cake discharged from the decanter centrifuge at 60% dry solids on average with a values ranging up to $180. This proved to be a significant advance in comparison with the traditional hydro-cyclones and other system, which involved hauling the slurry away at 25 to 30% dry weight solids. The reduction in process area and transport costs is also an attractive and valued factor. Whether or not the purchaser of the starch re-slurries the material for further treatment is irrelevant, but it is important to move the starch within a few days of production especially in hot weather (alternatively cold storage) to prevent deterioration of the product.
As results of the success of with potato chip manufactures machines were also installed at French-fry producers. Naturally, the starch yield is less in the case of straight cut french fries and represents approximately 0.3 – 0.5 % of the potato being processed as recoverable starch at 60% dry weight solids.
- Machine Wear Characteristics: No signs of wear to the bowl and screw conveyor.
- Process Issues: Gelatinized starch produced by the blanching process or by steam peeling, can cause process concerns with variations in the starch solids being discharged from the centrifuge:
- Starch 57 – 60 % dry solids
- Gelatinized (slimy) starch at 25 % dry solids
After testing several machine design changes and still experiencing two (2) different starch variations the client modified the potato fiber screen removing the gelatinized starch before reached the decanter centrifuge.
Abrasive peeling, slicing and or cutting potatoes and or other root crops causes the cells to release starch which is typically is rinsed off with fresh water before frying or taking the next process step. This potentially valuable starch is often left to wash down through the drain and to the plant wastewater treatment system where it will impact the Biological Oxygen Demand (BOD) and Chemical Oxygen Demand (COD) limits and treatment cost. Ideally many processors will want to find a solution for minimizing this added BOD / COD waste load on their treatment facility and recover the potentially more valuable starch selling to other processers specializing in starch refining or as animal feed.
Starch Dewatering Conclusion
The DRYCAKE DR Decanter Centrifuge is very well suited for starch dewatering. Where some manufacturers accept the starch as part of their wastewater effluent, there are several incentives to remove the starch upstream of plant or city wastewater treatment facilities:
- Sell recovered / dewatered starch
- Reduce wastewater treatment and effluent costs
- Recycle centrate to the pre-wash area
- Reduction of fresh water requirement
The decanter centrifuge separates the solids from the water and produces a dry friable cake material with an average moisture content of less than 40%, and the liquid phase will have had the majority of the solids removed which consequently provides is a dramatic reduction in the BOD / COD load on the plant or city treatment system providing a substantial savings in effluent charges. Other processing plant wastewater treatment applications require more traditional decanter centrifuge operation.
Wastewater / Effluent Treatment
Prior too many decanter centrifuge installations the typical processing plant effluent treatment program was a screen system with grit removal followed by a crude settling tank, primary clarifier, or lagoon. Typically underflow from a clarifier was thickened from 5% to 20% in a cone thickener prior to land disposal by tanker. The centrifuge is often installed to replace the thickener and cakes of up to 40 % were easily achieved without flocculent addition. Often the product is saleable to farmers as an animal feed additive. Suspended solids in the water discharged to the city are routinely reduced from 1,200 ppm to less than 300 ppm.

When steam peeling is used instead of abrasive peelers, gelatinized starch affects the cake and the dry solids content will not be as high but the resulting cake discharge at 20 to 25% is still a stackable and saleable product.
Machine Wear Characteristics
After approximately 10,000 hours, the effluent centrifuge was disassembled finding minor wear on the scroll and in the feed chamber. DRYCAKE now makes use of added wear protection on the scroll flights and a comprehensive tungsten carbide (or a similar material) protection liner in the feed chamber, to extend the scroll life beyond 12,000 hours.
Wastewater / Effluent Treatment Conclusion
The low speed decanter centrifuge is ideally suited for effluent derived from the potato process. Clients who have used belt presses have complained of high maintenance costs and excess water use in comparison with DRYCAKE DR Decanter Centrifuges and have also replaced rotary vacuum filters for similar reasons.
Potato Meal
Potato peel combined with reject potatoes, and substandard products can be pulverized into slurry. Water is then added and the potato meal slurry can be centrifuged to produce a cake of approximately 40 % DWS dry weight solids.
Potato Meal Conclusion
Potato meal commands a higher price than the potato waste in its original form. The proportion of cooked potato in the feed largely influences the dryness of the cake.
Potato flume and wash water recycling / cleaning (mud dewatering)
Use of the decanter centrifuge on a closed loop to the potato pre-washer or potato flume/transport water leads to the continuous removal of earth, mud, soil, potato debris etc. from the washing water.
The solids are discharged as a stackable cake at up to 50% DWS dry weight solids.
The cleaned liquid discharge is returned to the washer for reuse thus reducing the amount of water used at plant and allowing the washer to be run for extended periods before emptying.
The addition of a flocculent is not normally required but may be used to improve the superfine capture if needed, and achieve a centrate of < 100 ppm suspended solids.
Machine Wear Characteristics: In order to minimize wear, the bowl speed is reduced. The welded scroll wear protection operates for 15,000 to 20,000 hours before attention or tiled scrolls can be used to extend service intervals. No significant wear is found on any of the other parts.
Field Test Report / Potato Processing Combined Waste Effluent
Langley Separation and Process recently completed a successful wastewater / effluent demonstration test at a San Antonio, Texas snack food plant processing potatoes. The decanter centrifuge proved to be ideally suited for effectively reducing the BOD and TSS in the effluent generated from the potato washing, peeling and slicing processes. The machine also proved effective in helping free emulsified cooking oils for removal in the plants OWS system.
The test skid featured a small capacity decanter centrifuge fully equipped for easy, quick set-up on site for demonstration and application testing. Ancillary equipment includes controls, pumps, polymer systems, and sludge auger as well as connection hoses for a complete set-up.
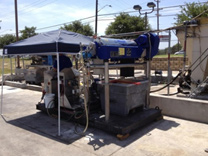
The pilot test unit basic components are:
- (1) DR test unit with 290mm diameter bowl
- (1) Automated PLC control system plus HMI
- (1) feed pump with a capacity of 0-35 GPM
- (1) Polymer dilution system with pump
- (1) dewatered solids screw conveyor (option)
The test was conducted over a one week period making multiple runs. The centrifuge feed was taken from a pit where several waste streams combined ahead of an oil water separator. The objective was to:
- Reduce solids
- Reduce BOD
- Help free up the fats and oils allowing the OWS to function more effectively
- Reduce solids volume hauling
- The results included an average reduction in BOD of 34%
- The results included an average reduction in TSS of 91%
- The cake was discharged from the centrifuge in a stackable cake
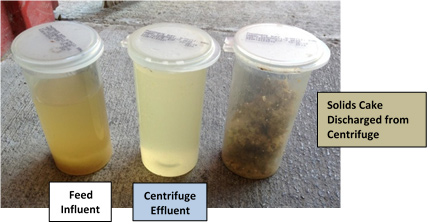
Plant Influent | Centrifuge Effluent | Reduction | |||||||
---|---|---|---|---|---|---|---|---|---|
Test # | BOD | TSS | FOG | BOD | TSS | FOG | BOD | TSS | FOG |
18 | 1930 | 2715 | 14.0 | 1119 | 216 | 29.7 | 42.0% | 92.0% | -112.14% |
19 | 1266 | 1084 | 12.9 | 1014 | 120 | 11.3 | 19.9% | 88.9% | 12.40% |
20 | 1033 | 1065 | 10.4 | 900 | 112 | 10.5 | 12.9% | 89.5% | -0.96% |
21 | 1359 | 2270 | 14.0 | 576 | 96 | 7.9 | 57.6% | 95.8% | 43.57% |
22 | 1119 | 824 | 12.9 | 891 | 140 | 10.3 | 20.4% | 83.0% | 20.16% |
23 | 1239 | 992 | 12.0 | 963 | 124 | 11.0 | 22.3% | 87.5% | 8.33% |
24 | 1770 | 4168 | 14.8 | 1386 | 256 | 16.2 | 21.7% | 93.9% | -9.46% |
25 | 3700 | 6890 | 10.4 | 984 | 196 | 14.8 | 73.4% | 97.2% | -42.31% |
Avg | 1677 | 2501 | 12.7 | 979 | 158 | 14.0 | 34% | 91% | -10.05% |
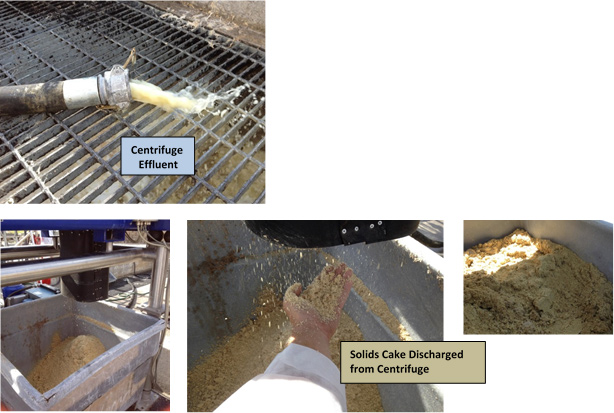
DRYCAKE DR Decanter Centrifuges offer numerous advantages for Potato and Root Crop Processing Plant Liquid / Solids Separation for Starch Recovery, Flume and Wash Water Clarification and Dewatering of Wastewater Sludge Applications:
Centrifuges provide unequalled starch recovery efficiencies
Centrifuges require a small amount of floor space relative to their capacity
Centrifuges require minimal operator attention
Easy to use and adjust with no full time operator required for continuous operation
Operators have low exposure to pathogens, aerosols, hydrogen sulfide or other odors
Centrifuges can handle higher than design loadings and the percent solids recovery can usually be maintained with the addition of a higher polymer dosage
DAF systems utilizing chemical polymers or flocculants can provide excellent water treatment results and relatively dry sludge cake when incorporating centrifuge technology to dewater the DAF sludge
Decanter centrifuge offers maximum flexibility and adjustability to meet process requirements for solids capture and dewatering solids discharge with simple adjustments
Wide range of slurry feed rates, feed solids concentrations and feed materials can be processed with coarse prescreening recommended to remove large and other miscellaneous debris
No filter media to blind-off
No screens or filter cloths to replace
Centrifuges are relatively easy to clean
All stainless steel product contact surfaces make the machines resistant to corrosion
Major maintenance items can be easily removed and replaced
Full scale pilot size machines available for testing and all pilot test data can be directly scaled to production feed rates

Mobile onsite application test units
LS&P and DRYCAKE maintain a full scale mobile decanter centrifuge test trailer for onsite application testing and centrifuge pilot testing. Portable systems feature a production model centrifuge mounted in a trailer with all the system controls and ancillary equipment such as pumps, polymer systems, and sludge auger as well as connection hoses for a complete set-up.
A typical one-week test program is specifically designed to evaluate performance, provide operational data, and determine optimal centrifuge capacity on representative material as well develop treatment experience with the centrifuge process. The test program will typically consist of a series of predetermined test runs designed to evaluate the cause-effect relationship between certain key performance parameters:
- Throughput vs. cake solids
- Throughput vs. solids capture rate
- Polymer addition /selection and effect on cake solids / solids capture rate
Langley Separation and Process can deliver complete skid mounted turnkey decanter centrifuge systems featuring custom automation / control panel, pumps, discharge chutes, pipe work, feed / receiving tanks, polymer systems, skid packages, platforms, and other accessories and options.
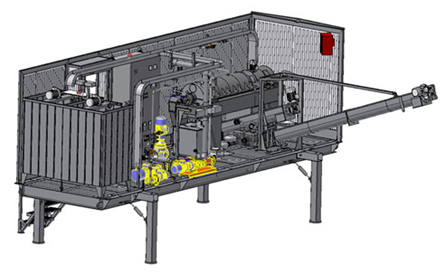
All DRYCAKE equipment is customizable to project specifications and can be provided with the following Explosion proof electrical options: Class 1 Div 1 and/or Class 1 Div 2.
In addition to our stationary decanter centrifuge systems, we offer mobile dewatering solutions for municipal and industrial applications for up to 400-gpm. These containerized systems include polymer make-up systems, feed pumps, flow-meters, cake discharge conveyors, piping, and integrated control panel. Container options include lighting, heating, windows, doors and stairs.
DRYCAKE also offers powder, emulsion, and combination powder/emulsion polymer make-up systems for continuous automatic operations.
DRYCAKE also offers Shaft-less Screw conveyors • Belt conveyors • Slewing conveyors • Horizontal bi-directional distribution conveyors • Vertical conveyors • Live bottom conveyors • Cake pumps