Municipal and Industrial Wastewater Treatment
Most water treatment plants (especially large plants) employ coagulation, sedimentation, and filtration and sludge dewatering processes.
Coagulant sludge is generated by water treatment plants using metal salts such as aluminum sulfate (alum) or ferric chloride as a coagulant to remove turbidity. The coagulant sludge consists of solids removed from the coagulated water, mainly hydroxide precipitates from the coagulant and material in the raw water. It may also contain water treatment chemical residuals such as polyelectrolytes, powdered activated carbon, activated clay, or unreacted lime. Alum is the most widely used primary coagulant in the United States. Activated silica, clay and/or a variety of polymers are used as coagulant aids. Alum coagulation sludge may contain aluminum hydroxide, clay and sand, colloidal matter, microorganisms including algae and planktons, and other organic and inorganic matter present in the raw water.
Lime Sludge Lime sludge is generated by water treatment plants using lime (CaO) or lime/soda ash (Na2CO3) softening. The quantity and composition of the sludge produced from softening may vary widely depending on whether or not alum or another coagulant is used either with or without a coagulant acid. As with coagulant sludges, lime sludges are removed from the water stream in the settling basin underdrain and in filter backwash wastewater. Residues from water softening are usually stable, dense, and inert. Lime sludge generally dewaters readily, depending on the ratio of calcium (Ca) to magnesium (Mg) and on the amount of gelatinous solids present in the sludge.
Dewatering Water Treatment Sludges
The most important factor in predicting DRYCAKE DR Decanter Centrifuge performance centers on the quality and characteristics of the sludge to be processed, which is dependent on two (2) primary factors:
- Treatment process used, particularly coagulants
- Quality of the raw water
Typical Sludge Types and Characteristics
Lime softening sludges: Cakes in the range 60% TS are usually obtainable. The limitation on machine capacity is often solids transport within the centrifuge. Low speeds are sometimes necessary to stay within scroll torque limitations.
Ferric hydroxide sludges: These dewater to 15-35%, depending on raw water turbidity, and the quantity of lime used in conjunction with ferric hydroxide.
Alum sludges: These sludges consist of a mixture of aluminum hydroxide, together with whatever organic and inorganic material is in the raw water. The inorganic materials dewater easily and the obtainable cake solids increase very rapidly with increasing raw water turbidity.
Turbidity: Wide ranging variations in turbidity depend on the water source and seasonal effects. Therefore, it is essential to take this into account when making performance estimates.
Flocculent addition: With the exception of lime softening sludges the addition of high molecular weight polyelectrolyte is necessary to achieve acceptable solids recovery in the centrifuge (usually 98-99%). Again, the quantity of polyelectrolyte required increases as the raw water turbidity decreases.
Centrifuge Capacity and Performance

Given the objective is usually to produce the driest practicable cake for transport/disposal purposes, the capacity of the centrifuge is influenced by the compressibility of the sludge. Within limitations on scroll drive torque, greater capacities can typically be achieved with sludges produced from high turbidity water sources and those containing lime. Thickened alum and ferric hydroxide sludges fed to the centrifuge can often vary greatly due to wide fluctuations in raw water turbidity. Together with the changing compressibility characteristics of the sludge, this usually makes the use of variable speed hydraulically controlled scroll drives a requirement in the centrifuge specification. An increase of several percent in the average cake solids is usually obtainable. Lime sludges are much more stable and the centrifuge can be operated with constant differential speed, provided the available scroll torque is adequate and the feed concentration does not vary greatly. Alum and ferric hydroxide sludges respond well to high-intensity dewatering under greater centrifugal forces given the compression effects produced by high speed centrifuges. Cakes 4-8% better than achievable with standard centrifuges can be expected.
Typical Decanter Centrifuge Performance
Coagulation Process | Thickened Sludge | Flocculent Dosage | Solids Recovery | Dewatered Cake |
---|---|---|---|---|
% TS | lbs/1000-lbs | DWS% | % TS | |
Lime Softening | 3-15 | 0-1 | 99+ | 55-65 |
Ferric Hydroxide | 1-6 | 1-3 | 99+ | 14-25 |
Lime & Ferric Hydroxide | 1-8 | 1-2 | 99+ | 25-40 |
Alum Turbidity 0-25 | 1-5 | 2-3 | 99+ | 12-18 |
Alum Turbidity >25 | 2-8 | 1-2 | 99+ | 20-30 |
A basic decanter centrifuge installation provides the flexibility to easily “adjust” operating parameters “on-the-fly” and produce the desired choice of thickened sludge concentrations. A simplified and typical flow-chart for sludge dewatering applications is shown below although not all process steps are present.


The DRYCAKE DR range of decanter centrifuges is ideally designed for these applications. Controlling the decanter centrifuge operating parameters optimizes the consistency of the discharged sludge cake and can be regulated to suit the disposal requirements.
DRYCAKE DR Decanter Centrifuges offer numerous advantages on water treatment sludge applications:
Centrifuges may offer lower overall operation and maintenance costs and can often outperform conventional belt filter presses
Centrifuges require a small amount of floor space relative to their capacity
Centrifuges require minimal operator attention
Easy to use and adjust with no full time operator required for continuous operation
Operators have low exposure to pathogens, aerosols, hydrogen sulfide or other odors
Centrifuges can handle higher than design loadings and the percent solids recovery can usually be maintained with the addition of a higher polymer dosage
Decanter centrifuge offers maximum flexibility and adjustability to meet process requirements for solids capture and dewatering solids discharge with simple adjustments
Wide range of slurry feed rates, feed solids concentrations and feed materials can be processed with coarse prescreening recommended to remove large and other miscellaneous debris
No filter media to blind-off
No screens or filter cloths to replace
Centrifuges are easier to clean
All stainless steel product contact surfaces make the machines resistant to corrosion
Major maintenance items can be easily removed and replaced
Full scale pilot size machines available for testing and all pilot test data can be directly scaled to production feed rates

Mobile onsite application test units
LS&P and DRYCAKE maintain a full scale mobile decanter centrifuge test trailer for onsite application testing and centrifuge pilot testing. Portable systems feature a production model centrifuge mounted in a trailer with all the system controls and ancillary equipment such as pumps, polymer systems, and sludge auger as well as connection hoses for a complete set-up.
A typical one-week test program is specifically designed to evaluate performance, provide operational data, and determine optimal centrifuge capacity on representative material as well develop treatment experience with the centrifuge process. The test program will typically consist of a series of predetermined test runs designed to evaluate the cause-effect relationship between certain key performance parameters:
- Throughput vs. cake solids
- Throughput vs. solids capture rate
- Polymer addition /selection and effect on cake solids / solids capture rate
Langley Separation and Process can deliver complete skid mounted turnkey decanter centrifuge systems featuring custom automation / control panel, pumps, discharge chutes, pipe work, feed / receiving tanks, polymer systems, skid packages, platforms, and other accessories and options.
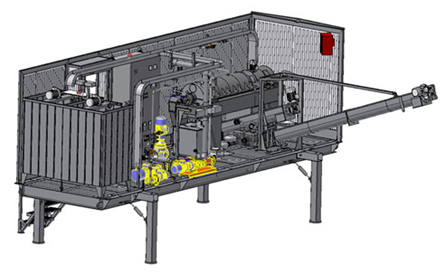
All DRYCAKE equipment is customizable to project specifications and can be provided with the following Explosion proof electrical options: Class 1 Div 1 and/or Class 1 Div 2.
In addition to our stationary decanter centrifuge systems, we offer mobile dewatering solutions for municipal and industrial applications for up to 400-gpm. These containerized systems include polymer make-up systems, feed pumps, flow-meters, cake discharge conveyors, piping, and integrated control panel. Container options include lighting, heating, windows, doors and stairs.
DRYCAKE also offers powder, emulsion, and combination powder/emulsion polymer make-up systems for continuous automatic operations.
DRYCAKE also offers Shaft-less Screw conveyors • Belt conveyors • Slewing conveyors • Horizontal bi-directional distribution conveyors • Vertical conveyors • Live bottom conveyors • Cake pumps