Parts & Service Program
At Langley Separation and Process we know how important it is for our decanter centrifuge, belt press, screw press and filter press customers operating valuable and complex plants, to optimize the mechanical reliability and maximum operational availability of such process equipment. We offer customized services including equipment retrofits, upgrades, refurbishments, training, testing and onsite dewatering equipment and process evaluations.
Langley Separation and Process is an OEM factory supported service and spare parts for Evoqua filter presses, JWI J-Press filter presses, J-MATE® Sludge Dryers and DRYCAKE DR Model Decanter Centrifuges, DRYCAKE Screw and Belt Presses plus all ancillary DRYCAKE equipment. Given our 40 years of experience working with decanter centrifuges, belt presses, screw presses and filter presses we also have the knowledge and capability to source spare parts and provide both field service and in-shop rebuilds for many other brands including:
Decanter Centrifuges
- Alfa Laval
- Hiller
- Humboldt
- US Filter
- Siemens
Learn more about our US Filter, Siemens and Hiller Parts & Service Program.
Belt Presses
- Ashbrook
- Andritz
- Envirex
- Enviroquip
- Pilgrims
- Sernagiotto / Sernatech
Filter Presses
- JWI
- Siemens
- US Filter
- Perrin
The following resources enable us to support you in achieving your service goals:
- Highly qualified and experienced service personnel
- Fast delivery of spare parts
- Standard and customized maintenance contracts
- First class repair service at our premises and or approved regional service centers
Approved LS&P Service & Rebuild Centers

- Canyon Lake, Texas (HQ)
- Houston, Texas (Primary Service Center)
- Indianapolis, Indiana
- Tampa, Florida
- Philadelphia, Pennsylvania
- Bakersfield, California
Whatever your needs, our professional staff will quickly and reliably answer your technical questions and help troubleshoot your specific requirements, schedule parts shipments, or arrange for an on-site service. Rebuilding your equipment is often a cost effective alternative to replacement and we will work within your budget. Field and/or in-shop rebuild services are designed to restore your dewatering equipment back to its original performance level including options to optimize your system with the latest technological improvements.
Belt and Filter Press Parts and Service
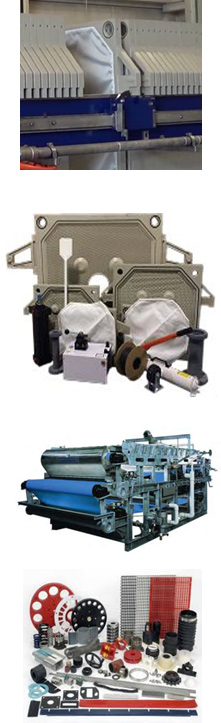
Maybe your belt or filter press has suffered a steady deterioration in performance over the past 5, 10 or even 20 years and you are not achieving the desired results such as:
- Your cake solids are not as dry
- Your effluent is not as clear
- Your throughput is lower
- Your maintenance costs are higher
Langley Separation and Process can assist with refitting your filter press with new plates, cloths, and/or expanding your filter press for increased capacity by supplying the necessary parts and or even providing a complete onsite rebuild service. We can customize a cost-effective maintenance program for your specific equipment, application, and environment that translates into lower maintenance cost and added years of worry-free operation.
Langley Separation and Process is an authorized Evoqua representative. Evoqua is the OEM for JWI J-Press, US Filter, Perrin, Siemens and other brands of filter presses plus JWI J-Mate sludge dryers.
Langley Separation and Process can also provide process engineering, trouble shooting and service for a variety of belt presses such as Ashbrook, Andritz, Envirex, Enviroquip, Pilgrms, and Sernagiotto / Sernatech.
With access to spare parts for many makes and models of belt presses Langley Separation and Process are able to expedite part orders for our customers as well as providing field service to replace bearing assemblies, seals, gaskets, rollers, doctor blades, steering valves, plows and many other parts. Often equipment can be modified or upgraded to improve reliability or increase the throughput enhancing the centrate quality and/or cake dryness. Whether it is a specialized modification, upgrade or complete mechanical rebuild that’s required our mechanical repair services are designed to minimize downtime and save you money.
Decanter Centrifuge Parts and Service

DRYCAKE DR Model Decanter Centrifuges and ancillary DRYCAKE equipment parts and service are readily available by contacting our staff in Canyon Lake, Texas or DRYCAKE directly on the North American toll free number. Customers also have access to the DRYCAKE DR Decanter Centrifuge factory service team hotline in Monteroberto, Italy.
In-stock fast spare parts delivery
DRYCAKE has an extensive stock of original OEM spare parts. This enables DRYCAKE to deliver the required original parts to the customer very fast – often even on the following day.
Maintenance contracts
As a convenience to our customers Langley Separation and Process offer annual DRYCAKE service contracts with authorized Service Technicians dispatched from both Italy and USA. Plus DRYCAKE has an established network of factory approved independent regional repair shops which serve as a supplemental alternative for long term equipment maintenance and repair. Most DRYCAKE contracts include the added benefit of a 10% discount on all spare and wear parts. In addition Langley Separation and Process and DRYCAKE will coordinate the complete time and service interval management as well as the corresponding inspection logbook entries providing customers optimum machine reliability and legal security.
Highly qualified service personnel
In addition to servicing DRYCAKE DR Decanter Centrifuges the Langley Separation and Process can also provide process optimization, trouble shooting and field service for other brands of decanter centrifuges such as Alfa Laval, Hiller, Humbolt, Sharpless, Siemens and US Filter. This service is founded on years of decanter centrifuge experience. Langley Separation and Process has access to OEM spare parts for many makes and models of decanter centrifuges are able to expedite part orders as well as provide field service to replace bearings, seals, gaskets, and many other parts. Langley Separation and Process can also provide maintenance contracts designed for the unique requirements of each customer to optimize the reliability and considerably extend the life of your machine.
First class decanter centrifuge repair and refurbishing services
Langley Separation and Process can also provide decanter centrifuge rotating assembly, rebuild, repair, refurbishing and complete reconditioning services. These services often include the following steps depending on machine condition at the time of service:
- Complete disassembly of decanter centrifuge
- Cleaning of all parts and components
- When necessary verify materials of construction using X-Ray Metallurgist Pro instrument
- Crack check key parts with Zyglo® liquid fluorescent penetrant inspection (Magna Flux)
- Media-blast all structural items and product contact surfaces
- Measurement of all critical tolerances and bearing fits
- Repair major sub-standard parts utilizing factory OEM prints and support and/or replace with new OEM parts
- Installation of complete head wall and scroll bearing seal assemblies
- Two-plane dynamic balancing of rotating assembly as required
- Scroll / conveyor inspection including feed zone and flighting repair as well as re-hard surfacing and re-tipping with flame sprayed wear protection or replacement of sintered tungsten carbide tiles
- Re-balance scroll / conveyor
- Repair and squaring of bearing pillow block mounting base locations
- Installation of rotating assembly
- Repair and refurbishment of covers and casings
- Perform four hour operational test-run of completed centrifuge repairs
- Verify and record dynamic balance
- Paint required items (customer to specify paint type & color)
- Re-skidded for shipment
Automation and centrifuge control panel component and operating program upgrades
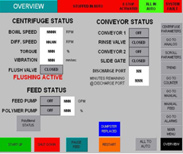
Langley Separation and Process provides process controls solutions and upgrades to increase centrifuge performance. We can help you increase production and profits with state of the art electronic controls, hydraulic drives and AC variable speed drive systems. Whether it’s a panel for a new machine or upgrade of an older machine, all aspects of automation and process controls are managed from design, engineering and construction through installation, integration and start-up.
- Allen Bradley, Siemens and other Programmable Logic Controllers (PLC)
- VFD drives, variable frequency, network interface and communications
- Operator Interface Terminals (OIT) and Human-Machine Interfaces (HMI)
- Data acquisition and trend analysis
- UL508A and NFPA approved industrial control panels
- Custom automation and process control optimization.
Learn more about our US Filter, Siemens and Hiller Parts & Service Program.