DRYCAKE Belt Press Equipment
Langley Separation and Process has many years of knowledge and process experience with the mechanical belt filter press, representing a complete selection of Belt Presses to serve a wide range of processing applications from conventional municipal waste and industrial sludge to high solids mineral dewatering. Additionally, Langley Separation and Process can also service, rebuild, support and source OEM parts for many belt press brands, such as DRYCAKE, Ashbrook Simon Hartley, Andritz, Komline Sanderson, Envirex, Roediger, Enviroquip, Pilgrim, US Filter, Siemens, Sernagiotto, and Sernatech.
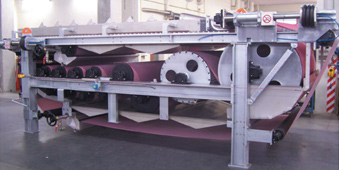

Belt Press Definition and Principle
Belt presses are a common type of mechanical dewatering equipment used to dewater most biosolids generated at municipal wastewater treatment plants and many industrial applications. Belt presses are used to remove water from liquid wastewater residuals and produce a non-liquid material referred to as “cake”. The Belt Filter Press is a broadly applicable product for dewatering municipal biosolids and industrial sludges. Since this is a continual process, it is effective on high-volume waste streams where a large production of low-quality filter cake is acceptable.
Many belt press designs and filtration processes are available, but all incorporate the following basic features: polymer conditioning zone, gravity drainage zones, low pressure squeezing zone, and high pressure squeezing zones. A belt filter dewaters biosolids or industrial sludges by applying pressure to squeeze out the water or liquid phase. Belt Filter Presses are available in a three-belt, a two-belt, and an extended gravity two-belt design. Advanced designs provide a large filtration area, additional rollers, and variable belt speeds that can increase cake solids.

For more details on how belt presses operate, and to learn more about belt press parts, components, and applications, see https://langleyseparation.com/equipment/belt-press-manufacturers/.
DRYCAKE Belt Press Technology
The latest DRYCAKE Belt Press technology has been developed to obtain higher flow rates and achieve cake dryness never reached by other belt presses with the same belt working width. This dewatering performance is thanks to new and innovative design features that include:
- A choice of 2 or 3 belt dewatering systems with standard, extended, or independent gravity zones for consistently high cake solids in varying sludge conditions
- When higher hydraulic sludge capacities need to be treated, the drainage zone is extended by installing a thickening stage before the actual dewatering process
- Increase of the effective filtration areas
- Innovative low pressure zone concept consisting of a big diameter perforated roll substitution in the traditional wedge area
- Effective high pressure zone (increase of pressure intensity and time)
- The possibility to install 5-7-9-11 rolls in final high pressure zone allows the machine to be configured per the application characteristics and required performance
The mechanical components have been sized to guarantee reliability even in severe conditions. The DRYCAKE Belt Press is suitable for all municipal and industrial applications.
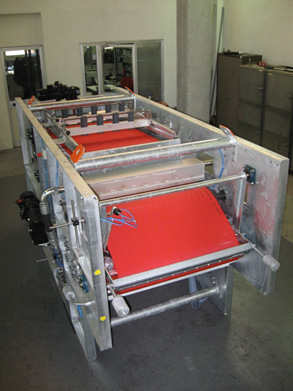
DRYCAKE belt presses are designed for dewatering both municipal and industrial sludges. The new modular frame concept combines outstanding performance with low capital costs, thus maximizing the costs/benefit ratio. These are suitable to treat a wide range of sludge types and concentrations: The “Standard” version of the machine is designed to dewater sludges with typical solid concentration, while the “Cascade” version combined with a belt thickener option suits very dilute sludges. The modular high pressure zone is also available with 8 rollers and can optionally be converted to an 11 rollers zone, adding 3 roller modules to further increase final sludge cake dryness.
A simple and cost effective Belt Press for dewatering of biological sludges, municipal and industrial features a compact enclosed design including a high pressure zone with 6/8 rolls. This design requires minimal space while providing efficient operational results. Frames are available in hot dip galvanized or stainless steel construction.
DRYCAKE Belt Press Advantages
- Automatic Operation
- High throughput capacities
- Superior cake dryness
- Belts of equal length
- Increased belt life thanks to constant torque dual motor system
- VFD controlled belt drive
- Flexible to the inlet sludge
- High quality construction
- Durable heavy duty design
- Reduced whole life cost
- Low energy consumption
- Low polymer consumption
- 7 to 11 High pressure rollers
- Hydraulic belt tensioning and centering
- Integrated belt washing pump
- Self-cleaning spray nozzles
- Sludge inlet reactor vessel or conical reactor distribution reaction tank
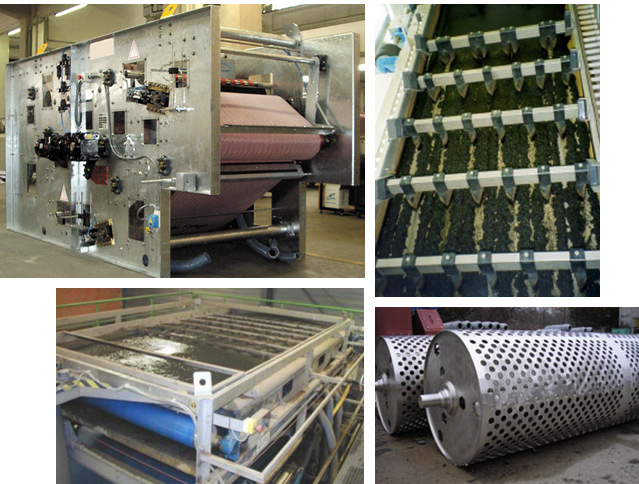
Common Belt Press Applications

- Municipal
- Raw
- Primary
- Primary & WAS
- Anaerobically Digested
- Primary
- Primary & WAS
- Aerobically Digested
- Primary & Activated
- WAS
- Potable Water Plant
- Alum Sludge
- Lime Softening Sludge
- River Water Silt
- Industrial
- Food Processing Wastes
- Pulp & Paper Wastes
- Chemical Sludges
- Pharmaceutical Wastes
- Industrial Wastes Processing Sludges
- Petrochemical Wastes
Selection of the basic machine is a function of the type of sludge and feed solids.
The design criteria for biosolids belt press applications are sized on the basis of weight or volume of solids to be dewatered rather than the wastewater flow to the plant. To determine what size or how many presses are needed, the wastewater treatment plant must:
- Determine the amount of primary solids that will flow through the plant per day
- Determine the amount of waste-activated or trickling filter solids produced per day
- Determine the volume of thickened solids to be dewatered per day
- Estimate the range of dry solids concentration in the feed
- Estimate future increases in solids production
Ancillary equipment for efficient operation of a belt press in a biosolids application includes:
- Polymer
- Mixing, aging, feed, liquid feed day tank
- Liquid residuals feed pump
- Odor control and ventilation
- Conveyor and/or pump to remove dewatered cake
- An enclosed area to load trucks or containers
DRYCAKE Belt Presses offer numerous advantages for sludge dewatering applications
- High quality structural frame materials and components for trouble-free, long lasting operation.
- Custom designed and built instrumentation/controls for guaranteed system integration
- Outstanding operating features and technology advances for higher throughput capacity, lower operating cost, and easier maintenance
- Feed section features that include flocculation tank and feedbox to uniformly apply sludge across entire width of belt while eliminating uneven distribution
- Gravity and wedge zone belt support bars are made of abrasion-resistant polyethylene and enhance dewatering by breaking surface tension of liquid
- High efficiency gravity zone with high rate drainage plows that work sludge to promote rapid drainage
- Lifting mechanism in the high rate drainage system facilitates raising and lowering of plows and elements into or out of service
- Self-bailing perforated first dewatering drum eliminates re-wetting of the cake through removal of water from inside the drum
- Variable wedge compression zone can be easily adjusted during operation to set a dewatering gap that maximizes material process rate and performance
- Rack and pinion tension controls links both ends of take-up roll to assure parallel belt movement and prevent uneven belt tension
- Heavy-duty carbon steel frame hot dipped galvanized after welding with 304 and 316 stainless steel frame options available
- Continuous belt washing is provided by fully enclosed wash stations with high pressure SS spray nozzles, internal cleaning brushes, special seals to eliminate noise and overspray, and access panels for convenient maintenance
- Replaceable polypropylene discharge blades extend over entire belt width and are counterweighted. Dry cake discharge is standard with optional discharge for thickened, pump able sludge
- Heavy duty split pillow block spherical roller bearings are all one size
- Sealed bearings protect from external contaminants and water
- Built in safety rope surrounds the entire system for emergency shutdown. Additional automatic shutdown controls stop the system for low pneumatic/hydraulic pressure, gross belt misalignment or broken belt, drive failure or low belt wash pressure
- 2-belt system with standard gravity zone and 2-belt system with extended gravity zone
- 3-belt system with independent gravity zone

DRYCAKE Belt Press Testing
Pilot units are essential for testing your process and proving out your specific dewatering application. On site pilot unit testing provides the opportunity to test a variety of conditions, configurations and operating parameters. Langley Separation and Process can assist with setting up and running the pilot equipment to determine the optimal belt press configuration and operating conditions.
- Confirm sizing requirements
- Assistance with filter belt selection
- Assistance with operating parameters optimization
- Selecting the correct configuration for your process
- Identifying parameters for custom controls and process engineering support
- Provide commissioning and start up activities or ongoing maintenance support
- Generation of cake and filtrate for further testing or downstream process optimization

Langley Separation and Process can arrange for a rental belt press. These pilot presses are available in a variety of sizes and come complete. All you need to do is add an air supply, connect your feed tank and start testing.
Langley Separation and Process can also assist with optimizing your current unit, planning a production change or working through a filter press problem. If you are experiencing issues with cake dryness or filtrate quality, making the changes necessary to investigate the problem can be difficult if you can’t take your belt press offline. So if you want to test different treatment chemistries, filter belts, or changing cycle parameters then renting a pilot unit makes perfect sense.
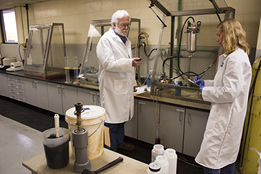
Langley Separation and Process can assist with submitting customer samples to one of several fully staffed, state-of-the-art laboratories for determining the most effective liquid/solids separation chemistries and techniques for each specific application. In addition to ensuring a better informed equipment purchase, this customer-focused service will also help you determine and maintain maximum performance of your belt press. To schedule services performed by one of our state-of-the-art testing labs, please contact Langley Separation and Process.
Belt Press Parts and Service

Langley Separation and Process can also service, rebuild, support and source OEM parts for many belt press brands, such as DRYCAKE, Ashbrook Simon Hartley, Andritz, Komline Sanderson, Envirex, Roediger, Enviroquip, Pilgrim, US Filter, Siemens, Sernagiotto, and Sernatech. Available parts include:
- Scraper blades & Doctor blades
- Center shafts
- Center barrels
- Drums
- Plows & Chicanes
- Agitators
- Vacuum system parts
- Multi-flex connectors
- Screw Conveyors
- Drainage Grids Division Strips
- Rollers & Pulleys
- Drainage Belts
- Sectors and Segments
- Tracking Systems
- Valves
- Pumps
- Wear Plates
- Bearing housings & liners
- End seals
- Worms & worm gears
- Seals
- Tanks
- Filter drivers
- Wash shower assemblies
- Spray nozzles
Langley Separation and Process can deliver individual filter presses and / or complete dewatering systems featuring custom automation / control panel, pumps, pipe work, feed / receiving tanks, polymer systems, mixers, skid packages, discharge augers, platforms and other accessories and options.
- Sludge thickening and storage tanks
- EQ tanks with vortex ring mixers
- Polymer and chemical addition systems
- Wastewater transfer and feed pumps
- Filter cake transport conveyors
- Dewatering Equipment Fundamentals (630K, PDF)
- Belt Press Operational Training 101 slides (2MB, PDF)
- Belt Press Mechanical Training 101 slides (2.7MB, PDF)