Belt Press Equipment & Manufacturers
Langley Separation and Process has many years of knowledge and process experience with the mechanical belt filter press representing a complete selection of Belt Presses to serve a wide range of processing applications from conventional municipal waste and industrial sludge to high solids mineral dewatering. Additionally, Langley Separation and Process can also service, rebuild, support and source OEM parts for many belt press brands, such as Ashbrook Simon Hartley, Andritz, Komline Sanderson, Envirex, Roediger, Enviroquip, Pilgrim, US Filter, Siemens, Sernagiotto, DRYCAKE, and Sernatech.
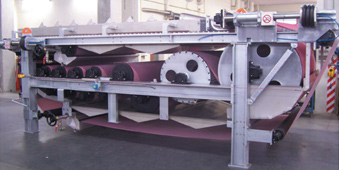

Belt Press Manufacturers and Models
There are multiple belt press equipment manufacturers throughout the world, and many common models available. Langley Separation and Process can help you acquire or service all the following major belt press brands.
- Ashbrook Belt Press
- Ashbrook-Simon-Hartley Belt Press
- Ashbrook Klampress Belt Press
- Ashbrook Winklepress Belt Press
- Ashbrook Type 85 Belt Press
- Ashbrook Type 890 Belt Press
- Andritz Belt Press
- Andritz SMX-S8 Belt Press
- Komline Belt Press
- Komline Sanderson Belt Press
- Komline Kompress Belt Press
- Roediger Belt Press
- Roediger Tower Press Belt Press
- Enviroquip Belt Press
- Enviroquip Series 3 Belt Press
- Enviroquip Series 4 Belt Press
- Enviroquip Series 5 Belt Press
- Sernatech Belt Press
- Sernatech Greenland Belt Press
- Envirex Belt Press
- Alfa Laval Belt Press
- Ovivo Belt Press
- Parkson Belt Press
- Aspen Belt Press
- Pace Belt Press
- Centrysis Belt Press
- Pinnacle Belt Press
- WBI Belt Press
- Sernagiotto Belt Press
- US Filter Belt Press
- Siemens Belt Press
- Phoenix Belt Press
- Textile Engineering Belt Press
- Eimco Belt Press
- Compositech Belt Press
- Flottweg Belt Press
- Sebright Belt Press
- BDP Belt Press
- Charter Machine Belt Press
- Carter Belt Press
- Vonroll Belt Press
- Hiller Belt Press
- Hiller-US Belt Press
- Bi Belt Press
Belt Press Definition and Principle
Belt presses are a common type of mechanical dewatering equipment used to dewater most biosolids generated at municipal wastewater treatment plants and many industrial applications. Belt presses are used to remove water from liquid wastewater residuals and produce a non-liquid material referred to as “cake”. The Belt Filter Press is a broadly applicable product for dewatering municipal biosolids and industrial sludges. Since this is a continual process, it is effective on high-volume waste streams where a large production of low-quality filter cake is acceptable. Typically, a belt filter press receives a slurry ranging from 1-4% feed solids and produces a final product of 12-35% cake solids. Performance depends on the nature of the solids being processed and dewatering biosolids and industrial sludges serves many purposes:
- Reducing the sludge volume, thus reducing storage and transportation costs
- Eliminating free liquids before landfill disposal
- Reducing fuel requirements if residuals are to be incinerated or dried
- Avoiding the associated issues with runoff from liquid land application
- Producing a material which has sufficient void space and volatile solids for composting when blended with a bulking agent
- Optimizing subsequent processes such as thermal drying
Many belt press designs and filtration processes are available, but all incorporate the following basic features: polymer conditioning zone, gravity drainage zones, low pressure squeezing zone, and high pressure squeezing zones. A belt filter dewaters biosolids or industrial sludges by applying pressure to squeeze out the water or liquid phase. Chemically conditioned solids sandwiched between two tensioned porous belts are passed over and under rollers of various diameters while increasing pressure is created as the belt passes over rollers which decrease in diameter.
Belt Filter Presses are available in a three-belt, a two-belt, and an extended gravity two-belt design. The three-belt press has an independent gravity zone with a more open belt for more rapid drainage of the volume of water. The extended gravity design has a longer gravity drainage zone. Most machines can actually be divided into three (3) zones:
- The gravity zone which drains free water by gravity through a porous belt
- The wedge zone where the solids are prepared for the pressure application
- The pressure zone, which applies medium then high pressure to the conditioned solids
Advanced designs provide a large filtration area, additional rollers, and variable belt speeds that can increase cake solids. The general mechanical components of a belt filter press include dewatering belts, rollers and bearings, belt tracking and tensioning system, controls and drives, and a belt washing system.

The belt press sludge inlet is supplied with a polymer mixing / conical reactor conditioning zone which is a small tank, approximately 75 to 250-gallons located on or within close proximity of the belt press. The gravity drainage zone is a flat or slightly inclined belt unique to each model. Solids are dewatered by the gravity drainage of the free water, which should yield a 5% to 10% increase in solids concentration in this zone. The free water drainage is a function of wastewater solids type, quality, conditioning, screen mesh, and design of the drainage zone. The low-pressure zone is the area where the upper and lower belts come together with the wastewater solids in between. This is sometimes called the “wedge zone,” because the feed solids are being sandwiched between the upper and lower belts. The low-pressure zone prepares the biosolids by forming a firm cake that can withstand the forces of the high pressure zone. In the high-pressure zone, forces are exerted on the solids by the movement of the upper and lower belts as they move over and under a series of decreasing diameter rollers.
Several key features enable a belt press to achieve substantially higher through-put capacities and produce dryer sludge cake solids:
- A choice of 2 belt or 3 belt dewatering systems
- A design that allows the 3 belt design to be a combination thickener and/or dewatering unit
- A polymer/sludge mixing conditioning system
- The use of the high rate drainage plow technology in the gravity zone
- A wedge section with an adjustable angle of conversion of the belts
- An easily adjustable, variable wedge compression zone that maximizes process rate and performance
- A large initial drum in the pressure/shear zone
- An extended length pressure/shear zone
- A high performance, larger to smaller drum pressure profile for higher cake solids concentration
- Larger standard filtration areas for greater process throughput and higher cake consistency
- A high rate drainage system that dramatically improves filtration rates
- High quality structural frame materials and components for trouble-free, long lasting operation
- Automated belt press operation supplied with the following options:
- Startup and Shutdown
- Level Control
- Flow Control
- Polymer Feed Rate
- DCS interfacing
- Alarms
- Diagnostics and Troubleshooting
Belt Press Components and Characteristics
Proper chemical conditioning is necessary to reach the highest dewatering performance. This reaction requires both an efficient mixing between the sludge and the reagent solution with sufficient time to allow flocculation before the dewatering stages. This process is occurs in a vertical mixer which contains a variable speed rotating shaft with stirring blades to enhance the mixing action. The mixer volume ensures the necessary reaction time. The flocculated sludge exits at the top of the mixing chamber and is discharged into the feeding box.
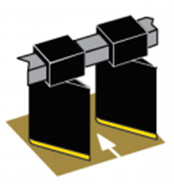
The machine configuration features a particularly long drainage zone which can handle high hydraulic flow rates even for a “difficult” sludge. In addition, the filtering belt is supported by polyethylene bars which help break the surface tension and help the drainage by gravity. Parallel rows of vertical plows can be fitted to further improve the pre-dewatering efficiency. Their shapes help assist the water drainage. The plows are assembled on stainless steel bars and are made of a plastic material with replaceable anti-wear plastic shoes.

The low pressure zone consists of an innovative roll system (wedging roll). This large diameter (1200 mm) perforated roll exerts a gentle and even pressure (typically approximately 0.10 to 0.15 kg/cm2) over the sludge for a longer retention time and creating further separation of the water. Roll parts in contact with the belt, are made of perforated sheet (either in stainless steel, or hot dip galvanized carbon steel or Rilsan® coated carbon steel). The separated water is removed through the belts.
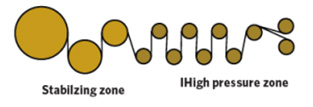
The high pressure zone consists of a sequence of rolls (from 5 up to 15). The two belts containing the sludge wind around them in “S” shaped configuration. The initial four rolls, the first being the wedge roll described above, feature progressively decreasing diameters along the working direction, to gradually increase the pressure on the sludge providing a stabilizing effect. All the following pressure rolls are of the same diameter, which increase the high pressure zone retention time improving final sludge dryness. The number of rolls in this last stage can vary depending on the application.

The mechanical stress over the rolls is reduced to a minimum by sizing them for a deflection less than 0.6 mm/m at the middle of the roll under continuous operation with 9 kg/cm linear tension on the belts and 4.5 m/min belt speed. This gives a longer life of the rolls, bearings and belts. The bearings are selected to guarantee a life of 100,000 hours. The rolls (apart from the perforated ones) are fully coated, including journals and stubs, either by 5mm Buna-N rubber (85±5 shore A hardness) or by Rilsan®.

Belt tension is maintained and controlled pneumatically. Increasing the tension raises the dewatering pressure applied both on the low and high pressure zones. The air bellows have the advantage of being elastic, thus transmitting the forces to the belts smoothly. They are joined to tensioning rolls by stainless steel rack shafts connected across the machine width for parallel motion. This system allows the belt tension to vary up to 10 kg/cm and to be adjusted without stopping the machine.

The belt motion is carried out by a variable speed twin motor system with each motor connected to an independent traction roll for the upper and the lower belt. This allows a constant torque on the belts with less stress and increased belt life. Great care was spent to minimize the spare parts costs so the upper and lower belts are designed to be equal length.
The frame is designed to guarantee steady long term performance and reliability of the machine. The maximum stress is lower than 1/4 of the frame’s material yield strength and the maximum frame deflection are rated for less than 2mm. The structural beams are in 510 carbon steel or can optionally be supplied manufactured from stainless steel or hot dip galvanized carbon steel.
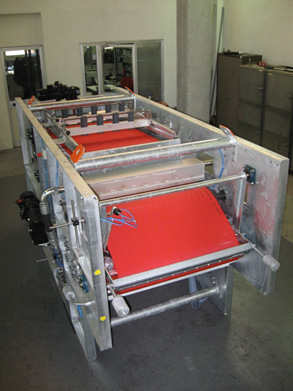
The belt presses are designed for dewatering both municipal and industrial sludges. The new modular frame concept combines outstanding performance with low capital costs, thus maximizing the costs/benefit ratio. These are suitable to treat a wide range of sludge types and concentrations: The “Standard” version of the machine is designed to dewater sludges with typical solid concentration, while the “Cascade” version combined with a belt thickener option suits very dilute sludges. The modular high pressure zone is also available with 8 rollers and can optionally be converted to an 11 rollers zone, adding 3 roller modules to further increase final sludge cake dryness.
A simple and cost effective Belt Press for dewatering of biological sludges, municipal and industrial features a compact enclosed design including a high pressure zone with 6/8 rolls. This design requires minimal space while providing efficient operational results. Frames are available in hot dip galvanized or stainless steel construction.
Belt Press Alternative Names & Terminology
While many people in the dewatering, separation and filtration industry refer to this equipment as Belt Presses, some use some additional or alternative terms, including the following:
- Rotary Press
- Vacuum Press
- Filter Press
- Roller Press
- Dewatering Press
- Separation Press
- Filtration Press
Common Belt Press Applications

- Municipal
- Raw
- Primary
- Primary & WAS
- Anaerobically Digested
- Primary
- Primary & WAS
- Aerobically Digested
- Primary & Activated
- WAS
- Potable Water Plant
- Alum Sludge
- Lime Softening Sludge
- River Water Silt
- Industrial
- Food Processing Wastes
- Pulp & Paper Wastes
- Chemical Sludges
- Pharmaceutical Wastes
- Industrial Wastes Processing Sludges
- Petrochemical Wastes
Selection of the basic machine is a function of the type of sludge and feed solids.
The design criteria for biosolids belt press applications are sized on the basis of weight or volume of solids to be dewatered rather than the wastewater flow to the plant. To determine what size or how many presses are needed, the wastewater treatment plant must:
- Determine the amount of primary solids that will flow through the plant per day
- Determine the amount of waste-activated or trickling filter solids produced per day
- Determine the volume of thickened solids to be dewatered per day
- Estimate the range of dry solids concentration in the feed
- Estimate future increases in solids production
Ancillary equipment for efficient operation of a belt press in a biosolids application includes:
- Polymer
- Mixing, aging, feed, liquid feed day tank
- Liquid residuals feed pump
- Odor control and ventilation
- Conveyor and/or pump to remove dewatered cake
- An enclosed area to load trucks or containers
Typical Belt Press Process Flow Diagram

Belt Press Testing
Belt press pilot units are essential for testing your process and proving out your specific dewatering application. On site belt press pilot unit testing provides the opportunity to test a variety of conditions, configurations and operating parameters. Langley Separation and Process can assist with setting up and running the pilot equipment to determine the optimal belt press configuration and operating conditions.
- Confirm sizing requirements
- Assistance with filter belt selection
- Assistance with operating parameters optimization
- Selecting the correct configuration for your process
- Identifying parameters for custom controls and process engineering support
- Provide commissioning and start up activities or ongoing maintenance support
- Generation of cake and filtrate for further testing or downstream process optimization

Langley Separation and Process can arrange for a rental belt press. These pilot presses are available in a variety of sizes and come complete. All you need to do is add an air supply, connect your feed tank and start testing.
Langley Separation and Process can also assist with optimizing your current unit, planning a production change or working through a filter press problem. If you are experiencing issues with cake dryness or filtrate quality, making the changes necessary to investigate the problem can be difficult if you can’t take your belt press offline. So if you want to test different treatment chemistries, filter belts, or changing cycle parameters then renting a pilot unit makes perfect sense.
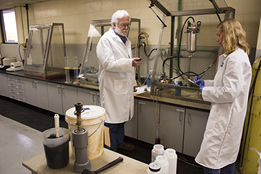
Langley Separation and Process can assist with submitting customer samples to one of several fully staffed, state-of-the-art laboratories for determining the most effective liquid/solids separation chemistries and techniques for each specific application. In addition to ensuring a better informed equipment purchase, this customer-focused service will also help you determine and maintain maximum performance of your belt press. To schedule services performed by one of our state-of-the-art testing labs, please contact Langley Separation and Process.
Belt Press Parts and Service

Langley Separation and Process can also service, rebuild, support and source OEM parts for many belt press brands, such as Ashbrook Simon Hartley, Andritz, Komline Sanderson, Envirex, Roediger, Enviroquip, Pilgrim, US Filter, Siemens, Sernagiotto, DRYCAKE, and Sernatech. Available parts include:
- Belt Press Scraper blades & Doctor blades
- Belt Press Center shafts
- Belt Press Center barrels
- Belt Press Drums
- Belt Press Plows & Chicanes
- Belt Press Agitators
- Belt Press Vacuum system parts
- Belt Press Multi-flex connectors
- Belt Press Screw Conveyors
- Belt Press Drainage Grids Division Strips
- Belt Press Rollers & Pulleys
- Belt Press Drainage Belts
- Belt Press Sectors and Segments
- Belt Press Tracking Systems
- Belt Press Valves
- Belt Press Pumps
- Belt Press Wear Plates
- Belt Press Bearing housings & liners
- Belt Press End seals
- Belt Press Worms & worm gears
- Belt Press Seals
- Belt Press Tanks
- Belt Press Filter drivers
- Belt Press Wash shower assemblies
- Belt Press Spray nozzles
Langley Separation and Process can deliver individual filter presses and / or complete dewatering systems featuring custom automation / control panel, pumps, pipe work, feed / receiving tanks, polymer systems, mixers, skid packages, discharge augers, platforms and other accessories and options.
- Sludge thickening and storage tanks
- EQ tanks with vortex ring mixers
- Polymer and chemical addition systems
- Wastewater transfer and feed pumps
- Filter cake transport conveyors
- Dewatering Equipment Fundamentals (630K, PDF)
- Belt Press Operational Training 101 slides (2MB, PDF)
- Belt Press Mechanical Training 101 slides (2.7MB, PDF)