VORT-X Ring Mixers
Langley Separation & Process has many years of sludge dewatering knowledge and process experience and we know how important feed preparation is for a successful operation. Whether your application features a lagoon, process pit or EQ tank that requires destratification and thorough mixing prior to dewatering, Langley Separation can provide a VORT-X Ring Mixer for the job. The new VORT-X Ring Mixer (VRM) is totally unique and robustly designed to meet the most demanding mixing applications by moving the mixing ring generator plate “up-down / up-down” which produce successive vortex rings that travel through the body of liquid creating an efficient naturally occurring homogeneous mixing process. This is affordable, energy efficient, low maintenance mixing technology for the most demanding applications. Langley Separation & Process can supply a single VORT-X ring mixer as well as design and install a complete customized turn-key mixing solution for your unique application or facility requirements.

Ideal for economically producing homogenous feed slurries from lagoons, holding pits, EQ equalization tanks as well as aerobic & anaerobic waste digester sludge to improve the process performance of downstream liquid/solid separation, filtration, and dewatering equipment such as:
- Screw Presses
- Belt filter presses
- Decanter centrifuges
- Filter presses
Mixers are also excellent for de-stratifying bulk liquid storage tanks at tank farms and/or prior to tank clean-outs for more efficient liquid processing and sludge dewatering.
The VORT-X Ring Mixer’s economical and energy efficient design make them incomparably affordable to purchase and operate. Compared to traditionally complex more energy intensive rotary mixers that spin blades to stir the liquid, the VORT-X Ring Mixer technology provides equivalent mixing with up to 80% less power consumption while also significantly minimizing maintenance and downtime. VORT-X Ring Mixers are an ideal solution for replacing other more costly mixing methods and equipment.

VORT-X Ring Mixers feature a ring generator plate fixed to the end of a hollow drive shaft that is stroked up down in a reciprocating motion at controlled cycle rate by the mixer drive head. This reciprocating up down motion of the generator plate orifice produces vortex rings that travel both upward and downward through the fluid body. The distance a vortex ring travels, and the region being agitated can all be controlled to affect the mixing process making the VORT-X ideal for many potential applications.
Mixing Mother Nature’s Way
VORT-X Ring Mixers (VRM) are the logical result of the realization that frequent mechanical production of naturally occurring vortex rings in a controlled manner will result in an efficient homogeneous mixing process. This mixing method was originally identified and researched by a university professor who worked to develop commercial use of vortex ring mixing technology more than 30 years ago.
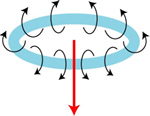
The VORT-X generates vortex rings by a reciprocating an orifice plate (Ring Generator Plate | RGP) to impulsively eject a slug of fluid through an orifice. This motion creates a stream of vortex rings above and below the orifice plate and radial toroidal rings from the Ring Generator Plate periphery. The mixing ring structure is called a “Toroidal Vortex” and in a typical vortex ring, the fluid particles move in roughly circular paths around an imaginary circle (the core) that is perpendicular to those paths. Unlike a sea wave, whose motion is only apparent, a moving vortex ring will carry the spinning fluid along. Just as a rotating wheel lessens friction between a car and the ground, the poloidal flow of the vortex lessens the friction between the core and the surrounding stationary fluid, allowing it to travel a long distance with relatively little loss of mass and kinetic energy, and little change in size or shape. Therefore, the stream of vortex rings transport fluid from the generating orifice to distant regions in the fluid which in turn creates an associated circulation and efficient mixing. Thus, the energy input to the fluid in achieving a homogeneous mixing process is consumed primarily in the transport process and not undue turbulence and excessive shearing.
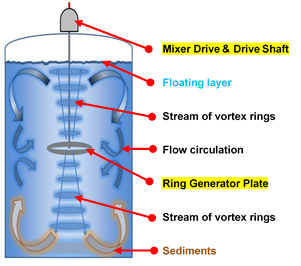
The vortex rings traveling up will push the mass of the liquid column out of the way leaving a slight trail in its wake. Once the vortex rings reach the liquid surface, they expand outwards and refold any floating sludge. Expanding to the sidewalls, the vortex ring will roll down until meeting the vortex rings traveling upwards.
The vortex rings traveling down push the liquid column mass out of the way as it is traveling down leaving a slight trail in its wake. Once the vortex rings hit the tank or vessel bottom the impact re-suspends any settled sediment or sludge. Expanding at the tank bottom, the vortex ring will roll up the sidewalls until meeting the vortex rings traveling downwards. Keep in mind that there will be a series of vortex rings following to prevent suspended solids from re-settling.

VORT-X Ring Mixers are easily adapted to most mixing applications and eliminate the problems typically associated with many mechanical mixers, rotary mixers, and other types of mixing frequently used throughout industry, waste treatment facilities, and anaerobic / aerobic digesters. The VORT-X provides high fluid mixing uniformity without dead zones and mixing can be easily controlled by adjusting the reciprocating up down motion cycle frequency (CPM), up-down stroke length, shaft length, ring generator plate size and / or location to provide the most efficient results.
- Extremely low energy consumption
- Rapid homogeneous mixing
- Low capital and operating costs
- Low maintenance
- Low shear
- Easy to control Improved process control
- No vessel baffles required – Freedom of vessel geometry
- Normally easy to retrofit
- Can be used in tall tanks and with various tank aspect ratios
- Excellent for sedimentary and floating materials suspension
- Not subject to abrasion, rags, or stringy debris
Ideal Applications Include:
- Routine mixing & agitation
- Equalization lagoon, pond, or tank mixing
- Waste lagoons, lakes, and pond destratification & aeriation
- Aerobic and anaerobic waste digesters
- Mixing shear sensitive materials
- Chemical addition and mixing
- Viscous fluids / Emulsification
- Solid suspension
- Ice prevention

Anaerobic digestion is highly dependent upon effective sludge mixing. VORT-X Ring Mixers are designed to provide powerful mixing, without accumulating stringy or fibrous material. This highly efficient mixing technology features low maintenance requirements and is configurable to suit the specific tank design and/or applications of new or existing digesters.
Alternative “Water Spider FLVM” Lagoon Mixing Unit
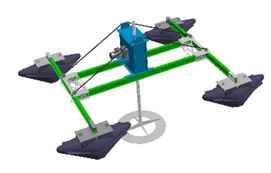
VORT-X ring mixers mounted on floating pontoons provide a cost-effective alternative for de-stratifying and mixing the lagoon contents to provide homogenous feed supply for the screw press, centrifuge, or belt press.
Sample Lagoon Mixing Set-up and Process Plan

Float (3) 5-hp VORT-X mixers with adjustable depth shafts and 48” diameter rings generator plates and use tethered cables to move them across the lagoon surface. Place (2) 300-gpm self-contained small diesel-powered trash pump units on the edge of the lagoon. Connect the pump inlet to a floating a submerged suction line and inlet basket strainer. Connect the pump discharge to an onshore centrifuge feed balance tank. Connect the centrifuge feed balance tank to the centrifuge feed pump. The centrifuge effluent gravity drains back into the lagoon.
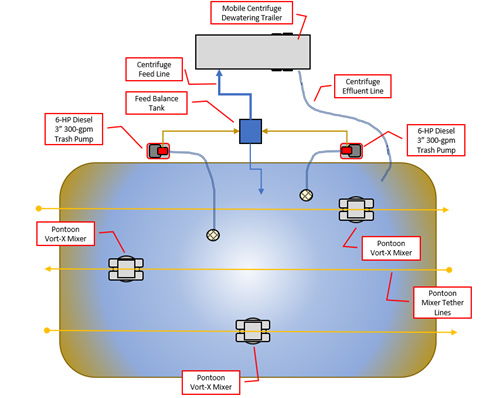
VORT-X Ring Mixer Mechanics

Mechanically the simple yet robustly designed mixer drive head utilizes a gearbox drive motor and connecting rod fastened to a tubular shaft that rides up and down vertically between two sets of four roller wheels supporting the shaft and submerged vortex ring generating plate. Wheel and shaft wear are minimized due to relatively loose tolerances and a ball joint connecting rod that tolerates the natural shimmy of the shaft. Additionally, all moving parts, rollers, bearings, and drive shaft assembly are located above liquid level and are not exposed to a hostile, submerged environment, resulting in a longer component part life. All moving parts, rollers, and rod end bearings can be easily and effectively lubricated and when moving parts need maintenance or even replaced, access is easy, and the entity being mixed does not need to be drained. The drive shaft does not pass through the basin or tank wall, so stuffing boxes and submerged drive chains or belts are not required, effectively eliminating such maintenance headaches. The cycle rate and vertical throw varies from 6” to 20” depending on ring generator plate size and application.

- Mixer drive head is easy to position and mount
- Mixer drive is relatively light weight
- Mixer drive head accommodates quick stroke length adjustments
- Mixer drive head is robustly designed for minimal maintenance
- Mixer drive automation and custom controls available
- Inject fluids or gaseous down the ring generator drive shaft tube for direct distribution into the mixing zone
VORT-X Ring Mixers are very robust and tolerant of debris, rags, stringy material contacting the Ring Generator Plate. The operation of the unit is also visible from a distance or can even be automated with a flashing light that illuminates with every stroke.
- Capable of mixing viscous fats, oils and greases
- Rag-less design and low maintenance cost
- Big energy savings compared to conventional mixing systems
- Capital and installation cost savings
- Suitable for both new and existing tanks
The Major Benefits of Applying VORT-X Ring Mixing Technology

Equal Mixing Capability @ 80%-85% Power Savings
The ability to reduce the power costs by up to 85% is a major factor and in many locations may qualify for grants and “green” energy savings credits.
No Tank Aspect Ratio Criteria Requirement
Propeller type mixers require careful analysis of the overall tank design to assure proper operation. Limits are placed on the tank diameter versus the tank height versus the style/amount of internal tank baffling required. Assurances must be taken to prevent internal vortices from damaging the mixer itself as well as making sure that the tank will indeed be mixed. The VRM will automatically adapt to any tank design, regardless of height or diameter. In fact, the tank designer can favor tank height as opposed to diameter which is typically far less expensive in initial capital costs and land usage.
Able to Address Rags
Propeller type mixers do not last long in a liquid environment that contains rag type solid debris. These rags can catch onto and interweave into the mixer blades – causing an unbalance, added maintenance and downtime. The performance of the VRM is completely unaffected by rag type solid debris of any size or shape.
Re-suspends Settled Solids into Solution
Costly cone bottom tanks are typically utilized for dealing with settled sludge. The amount of power along with the size of mixer needed to re-suspend sludge is typically cost prohibitive. The tank is taken off-line, emptied of its liquid contents, and then cleaned out of its settled sludge. The VRM can re-suspend settled tank sludge within minutes of start-up and maintain the solids suspension throughout its normal activity.
Refolds Floating Solids into Solution
Surface rakes and near-surface mixing is used for returning floating solids back into solution. This type of application requires an expensive style of process equipment along with its associated costs. The VRM can send a vortex ring in any direction including up into the liquid surface. The liquid surface will be agitated by the vortex rings which grab the floating scum folding it back into solution. If the end user prefers a quiet liquid surface, a deflector plate can be added to just below the liquid surface. This plate deflects the vortex ring and allows it to radiate outwards without disturbing the surface.
Non-Turbulent Mixing
Certain mixing styles such as flocculation require thorough mixing without causing any excess turbulence. Vortex ring generation can be controlled and slowed down to minimize turbulence while completely dispersing the chemicals.
Able to Function in Streams
Propeller type mixers are not able to last long in mixing within a crosscurrent stream. The stream pressure is different on the upstream blades versus the downstream blades – causing an unbalance and heavy maintenance. The performance of the VRM is completely unaffected by shallow flow rates of a crosscurrent stream.
Accurate and Fast Chemical/Gas Dispersion
It is extremely difficult to get chemicals dispersion completely on a time efficient basis. The closest seen is either use a solids contact clarifier (expensive) or adding the chemicals prior to a static mixer (one chance). With VRMs, the chemical or additive is easily piped directly to the zone of which the vortex ring is generated. When the ring is released, it is pregnant with the chemicals and/or additives – leaving a trail while traveling throughout the entire tank contents within seconds.
With this type of control:
- The amounts of chemicals/additives are minimized
- The time of completing the reaction needed by the process is optimal
- The tank volume can be strategically reduced due to faster reaction times
Model | HP | RG-Plate | Stroke | Shaft length | Standard Motor / Control Panel |
---|---|---|---|---|---|
VSM A 05-24 | 1/2 | 24″ | 6″ | up to 20′ | 480vac 60hz 3ph w/PLC/HMI/VFD |
VSM B 01-30 | 1 | 30″ | 7″ | up to 20′ | 480vac 60hz 3ph w/PLC/HMI/VFD |
VSM B 02-36 | 2 | 36″ | 8″ | up to 20′ | 480vac 60hz 3ph w/PLC/HMI/VFD |
VSM B 03-48 | 3 | 48″ | 10″ | up to 20′ | 480vac 60hz 3ph w/PLC/HMI/VFD |
VSM C 05-60 | 5 | 60″ | 12″ | up to 20′ | 480vac 60hz 3ph w/PLC/HMI/VFD |
VSM C 07-72 | 7.5 | 72″ | 14″ | up to 20′ | 480vac 60hz 3ph w/PLC/HMI/VFD |
VSM D 10-84 | 10 | 84″ | 16″ | up to 20′ | 480vac 60hz 3ph w/PLC/HMI/VFD |