DRYCAKE Screening Equipment
Langley Separation and Process offers the complete range of DRYCAKE screening equipment incorporating decades of mechanical knowledge and process experience with advanced mechanical features and superior processing performance.
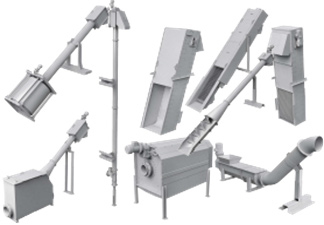
PERFOBASK: Screw-Screen
DSS screens are part of the DSS DRYCAKE Screw-Screen series and are designed to be installed into sumps, manhole chambers, underground chambers, pumping stations, etc. DRYCAKE vertical screens provide a solution to facilitate lifting, washing, dewatering, and compaction of solids for improving the performance and reliability of drainage systems.
Operating Principle
Screw-screens are integrated machines consisting of a screen, a shaft-less spiral and a compaction unit. During operation, solids within the incoming flow will progressively collect onto the screen mesh and cause it to gradually blind. The upstream water level will rise and at a predetermined level, the spiral will be activated. Brushes fixed to the periphery at the lower section of the spiral will then clean the screen mesh and convey the solids up to the compaction zone.
DSS screw-screens can be supplied either for direct installation into a channel or as a complete package inside a stainless-steel tank with or without the option of a bypass rake screen. Continuous bagging systems are available to receive screenings and abate odor, the screenings can then be sealed without any personal contact.
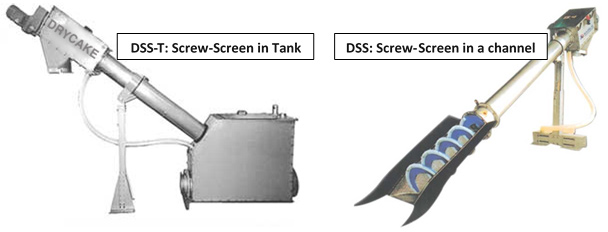
PERFOBASK VERTICAL: Vertical Screw-Screen
The Vertical Screw-Screen is designed to be installed into sumps, manhole chambers, underground chambers, pumping stations, etc. DRYCAKE vertical screens provide a solution to facilitate lifting, washing, dewatering, and compaction of solids for improving the performance and reliability of drainage systems.
Operating Principle
DSS-V vertical screens are part of the DSS DRYCAKE Screw-Screen series. DSS-V are integrated machines consisting of a screen, a spiral and a press unit. During operation, solids in the incoming flow will progressively collect onto the screen mesh. At a pre-set inlet water level, the spiral will be activated and convey the solids up to the pressing zone, brushes fixed to the periphery at the lower section of the spiral will clean the screen mesh. The solids or screenings are compacted and dewatered and depending upon the solid properties, a volume reduction of around 40% DS or greater can be achieved prior to discharging the screenings into a hopper or wheelie bin. Continuous bagging systems are also available to receive screenings and help abate odor. The screenings can then be sealed without any personal contact.
- DSS-V vertical screens can be supplied in variable lengths to suit individual applications. Vertical screens can also be designed for installation at inclined angles up to 50° from vertical.
- Flow Capacities up to 80-gpm depending upon perforation size, effluent and solids within the flow
- Fabrication: AISI: 304 or 316 Spiral: Mild steel or AISI: 304 or 316
- Screen basket size nominal 200, 300, 400, 500, 600 & 700 mm diameter
- Screen Perforation Sizes 0.25, 0.5, 1, 2 mm in wedge wire or 2, 3, 4, 5, 6, 7 & 10 mm perforated holes

Typical Applications
- Pump chambers
- Manholes, chambers and sumps
- Small sewage treatment works
- Municipal waste water treatment works
- Industrial effluent discharges
- Abattoirs, fish and other food processing plant
- Process liquor or fluid screening
- Sludge and scum screening
PERFODRUM DRD Rotary Drum Screw-Screen
DRD Operating Principle

DRD Rotary Drum Screw-Screens are integrated machines consisting of a screen, a screw conveyor and compactor. During operation, solids within the incoming flow will enter into the drum screen and progressively collect onto the screen mesh and cause it to gradually blind. The upstream water level will rise and at a predetermined level, the drum screen and screw conveyor will activate and rotate immersing a clean section of the screen into the effluent. During rotation the solids or screenings will become inverted and then fall into the screw conveyor. Spray nozzles and a roller brush fixed to the periphery of the drum screen will clean away any residual solids from the mesh. The screenings are conveyed, compacted and dewatered and depending upon the solid properties, a volume reduction of around 40% DS or greater can be achieved prior to disposing the screenings into a skip or wheel bin. A jet wash facility in the compaction zone will break down and remove fecal and other semi-solid or soluble matter and return it to the inlet flow. Additional jets can be installed in the transport zone to meet higher specifications of organic solids removal. Fecal matter washing efficiencies greater than 90% and screenings weight reduction of 50% can be achieved. The compactor and wash system can be omitted to suit requirements such as CSO applications where the screenings are returned to the downstream sewer.
DRD rotary drum screw-screens can be supplied for direct installation into a channel or as a complete package inside a stainless-steel tank with or without the option of a bypass rake screen. Continuous bagging systems are available to receive screenings and abate odor, the screenings can then be sealed without any personal contact.
- Flow Capacities Up to 555-gpm depending upon perforation size, effluent and solids within the flow Fabrication: AISI: 304 or 316 Spiral: Mild steel or AISI: 304 or 316
- Screen basket diameter nominal 600, 800, 1000, 1200, 1400, 1600, 1800, 2000, 2200, and 2400 mm
- Screen Perforation Sizes 0.5, 1, 2 mm in wedge wire or 2, 3, 6, 7 mm perforated holes
Typical Applications
- Pre-treatment of Municipal Wastewater
- Solids Recovery and Processing from Industrial Effluents
- MBR Membrane Bioreactor Inlet Screening
- Storm Overflows and Sea Outfalls

PERFOPLATE
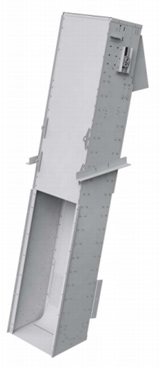
The PERFOPLATE is the ideal machine for the pre-treatment of the wastewater. The PERFOPLATE was designed with attention to the critical design points. For this reason, the PERFOPLATE has no submerged mechanical components. The motion of the chain is carried out only in the upper part, while in the lower zone there is no gear, but only one pair of sliding shoes. The PERFOPLATE is designed for simple installation in a concrete channel.
Operating Principle
The PERFOPLATE consists in a Stainless-Steel frame and is designed to be positioned in a channel with a 75° inclination. The screen is equipped with a stainless steel holed sheet with a spacing Ø between 2 and 10mm. The operation of the screen is automatic; the wastewater, passing into the screen, are filtered and once the water rise from the particles blinding the perforations the level reach the pre-set level, automatically activates the cleaning system of the filter screen. The brushes perform the cleaning and also the transport operation until discharged at the top. A gear-motor actuates the brush mechanism transmission.
- The PERFOPLATE can be manufactured in Stainless Steel AISI304-316 and is fully customizable according to the customer needs in addition to the standard range.
- Number of Brushes [2-6]: 2 brush standard plus one for every 3 feet in height to a maximum of 6.
- Installation Angle: 75˚Installation angle standard 80 & 90˚ installation angles available
- Standard Control and Instrumentation: DRYCAKE MICROLOGIX
- Control Panel Enclosure: NEMA 4X Stainless Steel
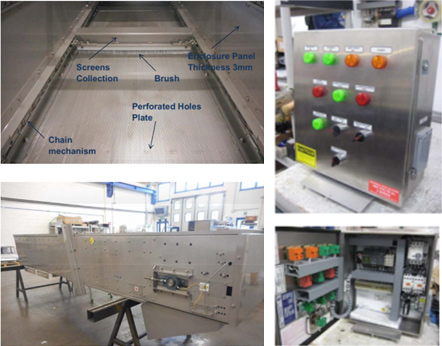
DBS: Vertical Bar Screen
For Pre-treatment of Municipal Wastewater and Recovery & Solids Processing from Industrial Discharges
Screen Characteristics
- Screen is composed of bars obstructing the solids present in the effluent.
- Cleaning of the screen is achieved by means of 2 rakes with teeth moved by 2 chains.
- Translation speed of the teeth: 5÷6 m/min.
- Inclination of the screen compared to the vertical: 15°.
- Spacing from 12 up to 60 mm.
- Frame is made with metal plates with a thickness of 3-4 mm.
- Gear motor shaft and crowns are manufactured in micro alloy steel.
- Translation chains type rollers chains are manufactured in stainless steel AISI 304 or AISI 316.
- Cleaning system is made in stainless steel AISI304 or AISI 316. The cleaning system crawls on the upper surface of the rake, causing the removal of the screenings conveyed from the same rake.
- Discharge chute: the discharge chute is manufactured in stainless steel AISI 304 or AISI 316.

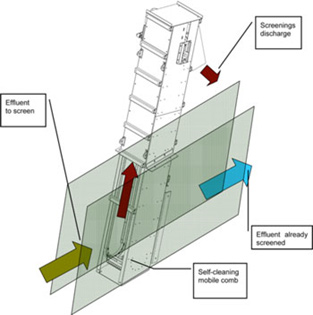
DBS Specifications
Screen type | Vertical Bar |
Screen Bar Spacing | 12 to 60-mm |
Maximum Flow | 2650 gpm |
Minimum Channel Width | 15.75″ |
Maximum Channel Width | 118″ |
Minimum Channel Height | 30″ |
Maximum Channel Height | 295″ |
DSW Screen Washer Compactor Press
The washer press is designed and dimensioned to wash and reduce the weight and volume of low liquid content screenings coming from an upstream screening source. The unit can be placed directly under a screen or fed with a conveyor. The screenings enter the unit through the inlet hopper. The screw presses the screenings while transporting them to compaction zone. The screenings are compacted and discharged into a hopper or bin for removal. The extracted liquid from compaction drains out a wedge wire or perforated basket and into the effluent discharge pipe.
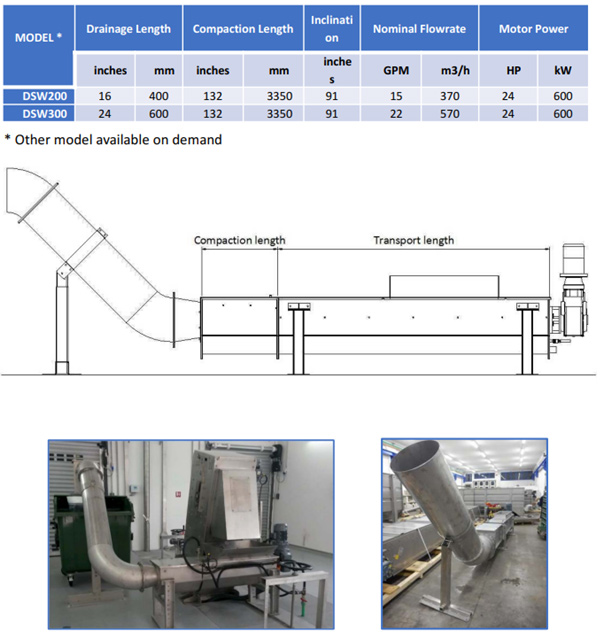
DSW Screen Washer Compactor Press
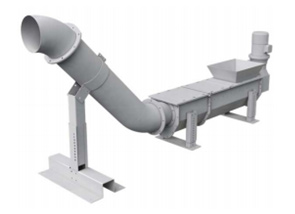
- Automatic operation
- Easy installation
- High screenings compaction up to 60%
- No submerged mechanical components
- Manufactured in ANSI 304 and 316
- Welding pickled and passivated for corrosion resistance
- Fully removable covers for hygienic encapsulation
- Disposal cost reduction
- Low and easy maintenance
- Washing provides 90% of organics removal
- Compaction reduces disposal volume as much as 60%

DRYCAKE TWISTER and SEDITANK
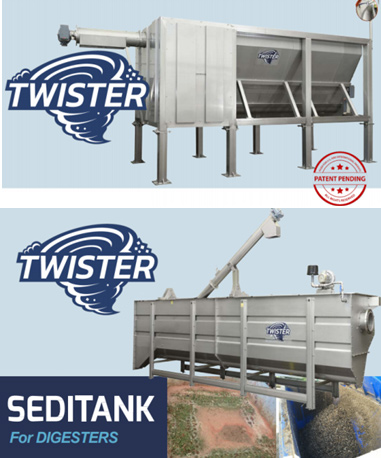
Langley Separation and Process offers the new DRYCAKE TWISTER De-packager and Organic Separator incorporating decades of mechanical knowledge and process experience with advanced mechanical features and superior processing performance.
The disposal of organics and food waste materials has become a problem for the entire world. New regulations require organics to be diverted or ban completely from landfills sites, as well as incinerators. Anaerobic digestion has become a popular alternative solution worldwide over the last years. The produced biogas can either be used to generate electricity or even condensed into CNG for use as fuel for trucks and vehicles.
The TWISTER De-packager and Organic Separator provides an economical organics separation and treatment process. The concentrated organic matter output is suitable for anaerobic digestion or can be used as a solid component for composting. The separated packaging material can be used for combustion or recycling.
The TWISTER De-packager and Organic Separator is primarily fed unsorted municipal waste, SSO, bio-waste from catering, supermarkets and shops, spoiled vegetables (even in paper, plastic or wood packaging), expired food or defective batches, food and beverages in cartons, cans or even in glass containers. For dry foods (e.g. biscuits), water is added to the separation or combined with other liquid and/or aqueous waste. The TWISTER De-packager and Organic Separator eliminates manual sorting and laborious unpacking of bio-waste from the packaging. The TWISTER discharges a solid waste material (food wrappers, plastic bags, fabrics, crushed boxes, etc.) that is only damp due to the centrifugal force of the process that removes the excess the liquid phase. The separated solid waste can be incinerated or recycled. The separated organic biomaterial phase is discharged as in a pasty to full liquid form.
A SEDITANK can be employed following the TWISTER De-packager and Organic Separator to clean the liquid phase removing heavy particles (glass, sand, etc.) and collecting floating residuals and packaging debris from the surface of the liquid organic biomaterial portion.
The innovative design of the TWISTER is the result of high experience in the field of pre-treatment and filtration and has been optimized following extensive testing of different scenarios to optimize organic capture for the best energy recovery. The optimized shape of the drum openings increase the open area considerably guaranteeing the passage of the organic fraction. This considerably reduces the use of clean water in order to dilute the organic material itself.
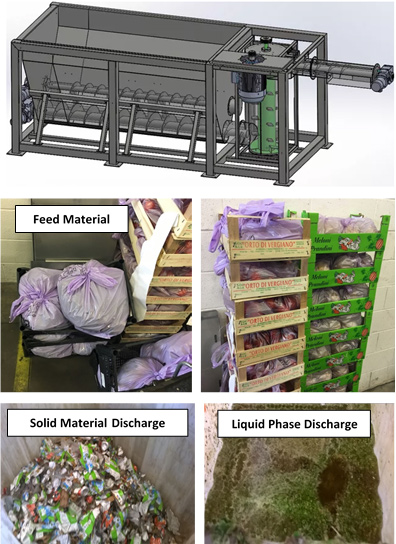
The TWISTER’s stainless steel design allows easy machine sanitation and ensures long service life. The electric motors are TEFC / IP68, so the machine can be cleaned using a pressure washer. The rotor is made of wear-resistant steel blades driven by a durable toothed belt. The machine is low-maintenance and only requires greasing. The TWISTER has low power consumption thanks to the use of electric frequency drives. The TWISTER has two screws in the hopper that counter rotate against each other. The upper screw acts as a bag opener and prevents bridging of the material fed into the hopper. The lower screw crushes the material and feeds it into a vertical drum with fine perforations in the drum wall. In this drum, the rotor reduces the bio-waste like a blender. The rotating blades simultaneously form a whirlpool (TWISTER) effect that pushes the pasty liquid component through the openings in the drum wall. The pasty liquid drains out of the drum or is then pumped out for further processing. The comminuted solid debris are pushed upward by the rotor and discharged from the drum into the discharge screw. Due to the high centrifugal force exerted on the solid debris, it is discharged practically free of water. It is advantageous to include the TWISTER-SEDITANK in the downstream production line if there is residual glass, sand, etc. in the liquid phase. These machines are an effective means of streamlining the disposal of waste and maximizing digester operation with efficiently prepared waste.
DRYCAKE TWISTER De-packager and Organic Separator and SEDITANK Advantages:
- All-stainless steel design
- Simple sanitation
- Automatic operation
- Low maintenance design
- No grinding or squeezing
- Direct drive of the auger screws
- A second auger screw prevents the formation of material bridging
- Rotor with interchangeable blades made in hardened material
- Low power consumption
- VFD driven rotor in order to adapt to varying products
Langley Separation and Process also offers DRYCAKE Shaft-less Screw conveyors • Belt conveyors • Slewing conveyors • Horizontal bi-directional distribution conveyors • Vertical conveyors • Live bottom conveyors • Cake pumps