DRYCAKE DSP Screw Press
Langley Separation and Process offers the complete range of DRYCAKE DSP Screw Presses incorporating decades of mechanical knowledge and process experience to provide an effective, low-maintenance solution for continuous solids thickening and/or dewatering with advanced mechanical features and superior processing performance. With over 100 DRYCAKE DSP Screw Press references worldwide, Langley Separation and Process has a proven solution for your dewatering needs.

DRYCAKE Screw Presses
The DRYCAKE DSP Screw Press provides a unique, cost effective economical solution for either sludge thickening or dewatering of municipal and industrial sludges. Low capital and operating costs as well as low maintenance costs were fundamental to the DRYCAKE DSP Screw Press design objectives and has culminated with the development of a highly cost-effective process. Sludge thickening up to 15% DS or, sludge dewatering up to 25% DWS are attainable with significant operational and energy savings while reducing sludge removal and transportation costs. Systems can operate automatically or manually as well as either continuous, or intermittently for batch processing. Various manufacturers’ flocculants may be used and the system can be supplied with or without preparation plant to suit requirements.
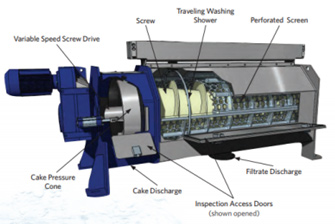
A screw press separates liquids from solids by continuous gravitational drainage. Screw presses are often used for materials that are difficult to press, for example those that tend to pack together. The screw press squeezes the material against a screen or filter and the liquid is collected through the screen for collection and use. The specific details of the design of a screw press depend on the material. The length and diameter ratio of the screw press also depends on the material. Screw presses feature stainless steel wetted parts and the screen casing is split to simplify screw removal and minimize footprint requirements. Perforated screens allow for tight tolerances and improved performance over wedge-wire screens. Low wash water requirements with cleaning cycles typically performed once per day for 3 to 5 minutes, plus dewatering operations do not need to be suspended during cleaning.
DRYCAKE Screw Press Operation
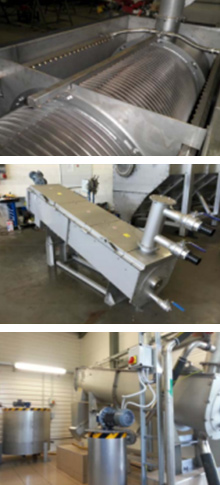
The DRYCAKE DSP Screw Press consists of static circular drums with internal screw conveyor. The drums are fabricated in stainless steel using various size special wedge-wire screen profiles with large surface to obtain optimum liquor drainage characteristics. The sludge is fed into the machine via pump or inlet chamber or feed hopper and into a cylindrical 250 micron wedge-wire drum where it conveys by spiral movement. The auger shaft is tapered with a smaller diameter on the inlet side and larger diameter on the discharge side and features a VFD controlled variable speed drive. The auger shaft transports the solids towards the drum discharge as the space between the auger shaft and the drum. The sludge retained in the drum is subjected to continuous movement and progressive compaction applying the desired effect of releasing more liquor to drain. The counter-pressure of the cone against the cake discharge maximizes the drying effect. Eventually the solids will pass into the discharge section and to the outlet where it can be collected into a container or conveyed for eventual disposal. Liquor continuously drains through the drum wedge-wire screen and gravitates to the filtrate outlet where it can be discharged or returned for treatment.

The cleaning system of the drum is provided by brushes installed on the external surface of the screw conveyor and a motorized washing system covering 70% of the drum surface without need for higher water consumption. Spray nozzles provide intermittent wash to the screen sections, however with inlet sludge solids content ≥ 1.5% DS, washing will not be necessary and water consumption is negated.
Sludge Dewatering and Thickening
With screw rotation less than 20 rpm, the DRYCAKE Screw Press conveys flocculated sludge very gently without high velocity shear, using low energy input and therefore will have an excellent recovery rate for all sludge types. Typically polymer addition is required for flocculation of the sludge and for best capture rate and dry cake and flocculated sludge is treated gently as flocculent utilization is kept low. The inlet sludge flow rate, polymer dosing rate, good flocculent formation and inclined angle determines the optimum final dry solids concentration and filtrate quality operating efficiency.
The quality of treatment will depend upon sludge type, temperature, selected polymer mixing and adequate flocculation time. Typical polymer usage for waste water sludge varies from 0.3 to 7.0 kg/ton DWS. In general sludge thickening requires less polyelectrolyte then sludge dewatering. Automated polymer preparation and dosing systems along with the option of a flocculation reactor can be supplied with a DRYCAKE DSP Screw Press.

When applied to sludge thickening, the same DRYCAKE Screw Press models are capable of processing increased inlet sludge flows over the above sludge dewatering capacities and higher, determined by the incoming sludge concentration and the final sludge dry solid content requirement. Wash Water Wash water is standard throughout the DRYCAKE Screw Press range; however with inlet sludge concentrations over 1.5% DS, washing will not necessarily be required but may be useful for periodic cleaning purposes.
DRYCAKE Features Five Standard Models:
Model | Drum Diameter (mm) | Motor HP | Inlet Sludge Flow @ 1%DS | Inlet Sludge Flow @ 3%DS | Filtrate Quality |
---|---|---|---|---|---|
DPS 200 | 200 | 1/2 | 4.5-GPM | 3.0-GPM | <400mg/l |
DPS 400 | 400 | 3/4 | 9.0-GPM | 6.0-GPM | <400mg/l |
DPS 400L | 400 | 3/4 | 12-GPM | 8.0-GPM | <400mg/l |
DPS 700 | 700 | 1.5 | 21.0-GPM | 15.0-GPM | <400mg/l |
DPS 900 | 900 | 2.0 | 26.0-GPM | 21.0-GPM | <400mg/l |
The design of the DRYCAKE Screw Press facilitates installations to be either inside buildings or outside without any sheltering, allowing direct disposal of thickened or dewatered sludge to a container or holding tank.

DRYCAKE Screw Press Advantages
- Automatic operation
- Simple mechanized operation
- Low speed operation
- High solids capture
- Low shear – excellent recovery of all sludge types
- Low energy consumption
- Innovative washing system
- No rotating synthetic filter cloth requiring periodic care
- Non-clogging even with fibrous materials
- Easy operation
- Continuous operation
- Compact, low space requirement
- High quality
- Manufactured in Stainless Steel AISI 304 or Optional 316
- Welding pickled and passivated
- High reliability and long asset life
- Simple installation
- Dewatering and discharge in one equipment
- Easy remove-able covers for hygienic inspection
- Odor and insect containing covers
- Low maintenance
Skid Mounted, Mobile and Complete Customized Screw Press Systems
Langley Separation and Process can deliver complete skid mounted turnkey screw press systems featuring custom automation / control panel, pumps, discharge chutes, pipe work, feed / receiving tanks, polymer systems, skid packages, platforms, and other accessories and options. All DRYCAKE equipment is customizable to project specifications and can be provided with the following Explosion proof electrical options: Class 1 Div 1 and/or Class 1 Div 2.
DRYCAKE also offers powder, emulsion, and combination powder/emulsion polymer make-up systems for continuous automatic operations. These polymer make-up systems are designed with proper aging time without the need for post dilution, thus increasing the polymer efficacy. Our systems are able to prepare concentrations between 0.05 to 0.5%. DRYCAKE polymer systems are made in stainless steel.
DRYCAKE also offers Shaft-less Screw conveyors • Belt conveyors • Slewing conveyors • Horizontal bi-directional distribution conveyors • Vertical conveyors • Live bottom conveyors • Cake pumps