Filter Presses – Full Circle Water, JWI, J-Press, US Filter, Perrin, Siemens
Langley Separation & Process has many years of mechanical filter press knowledge and process experience. Filter presses have long been industry proven as the technology of choice for a wide variety of industrial and municipal treatment dewatering applications that require separation between a liquid and solid suspension to produce a clean filtrate and dry cake solids. Langley Separation & Process represents filter press manufacturer and system integrator Full Circle Water. Full Circle Water offers a variety of state-of-the-art automated filter presses for use in countless applications and can engineer and install custom designed turnkey dewatering systems.
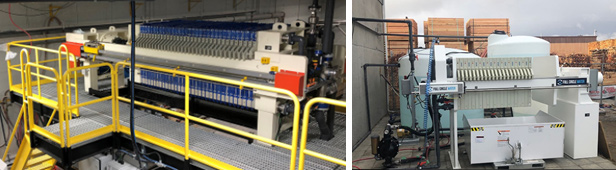
Full Circle Water also offers trailer mounted portable wastewater filtration systems that can process slurry and clarify water on your job site. FCW trailers come full equipped with chemical feed, mixing, air sparging, and filtration options to dewater your sludge effectively and efficiently. These mobile systems can clean wastewater produced from a variety of sources and processes that produce slurry in the field and recycle clarified water back to your application for re-use. Full Circle Water’s portable trailers allow slurry processing to be done onsite in real time, which greatly reduces transportation and disposal costs.
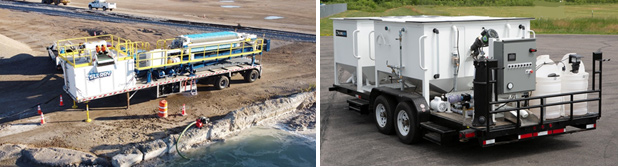
Filter Press Definition:
The primary usage of a filter press is as a “fixed volume, batch pressure filter” built to hold a specific quantity of solids. The term “batch” refers to the fact the cycle must be stopped to discharge the collected “filter cake” prior to restarting a cycle. “Pressure” is created by the feed pump in the separation process. The filter press may also be used as a “polishing” filter to remove minute solid particles from an influent or effluent stream. In these applications the press is not sized for the quantity of solids holding capacity but for maximum filtration area and hydraulic capacity. When used as a polishing filter, a dry filter cake is not generally developed and when the flow rates drop to an unacceptable level, the cycle is stopped. Another common use for a filter press is as a “variable volume” filter that uses a filter plate known as a diaphragm or membrane plate. This type of plate has a flexible drain-field which when sealed around the edges forms an integral bladder or diaphragm that may be inflated to physically press additional liquid from the filter cake. This process can significantly reduce the typical elapsed time for a press cycle and produce a dryer cake and more consistent cake dryness from cycle to cycle.
The Principle:
The pressure forcing the slurry (typically 100-psi, but up to 900-psi [7 to 60-bar]) is generated by a feed pump either a positive displacement or centrifugal pump. With a gravity drain on the filtrate side of the press, a pressure differential between the feed pressure and the gravity discharge is created across the media and the filter cake solids as the cake thickness increases. It is this pressure differential, not just the feed pump pressure, that causes the filtering action to occur. Solids within the slurry will flow to the area of cake development with the lowest pressure differential, resulting in a filter cake that builds uniformly over the drain-field on either side of the chamber walls. This fill cycle continues until the filter cake forming on the chamber walls bridges at the center, completely filling the press with solids and ending the filtration process. The hydraulic closure of the press is then retracted and the individual filter elements are separated discharging the filter cakes by gravity into an appropriate receptacle.
Process:

During operation the slurry is pumped under pressure into the press chambers through the manifold at the stationary head of the filter press. As each chamber fills with slurry, the liquid passes through the cloth medium, across the drain-field, through the drain ports and exits via gravity from the corner discharge ports. The prime function of the filter media is to provide a porous support structure for the filter cake to develop and build upon. Initially, some solids may pass through the cloth media causing a slight turbidity in the filtrate, but gradually the larger particles within the slurry begin to bridge the openings in the media reducing the effective opening size. This allows smaller particles to bridge these reduced openings initiating the cake filtration process. Once a layer of solid particulate achieves a 1 to 2 mm in thickness, this “precoat” layer serves to separate out finer and finer particles as the cake builds in thickness, yielding a filtrate that is very low in turbidity.
A Filter Press has two principal components:
- Skeleton
- Filter pack
This is true for all filter presses of the regardless of design including both the sidebar and overhead plate suspension type filter presses.
Filter Press Components:
The skeleton has one primary function which is to hold the filter pack together against the pressures developed internally during the filtration process. The terms used to describe the skeleton may vary slightly from manufacturer to manufacturer, but the sub-components remain essentially the same:
- Stationary head
- Follower head
- Hydraulics
- Manifold
The following are important considerations when selecting and/or sizing a filter press:
- Volume per day
- The volume of slurry generated per day is also used in the calculation of the mass of dry solids per day to be dewatered.
- Hours of filter press operation per day
- The size of the filter press is also determined by the hours per day it can be operated. The cake from a filter press can be dropped 6 times per 24 hour period with a 4 hour press cycle. If the filter press is operated only 12 hours per day it can only run three 4 hour cycles which results in the size of the press being 2 times larger.
- Specific gravity of slurry
- The specific gravity is the weight per unit volume (i.e. pounds/gallon) of slurry and can significantly vary from application to application. It is used to accurately calculate the mass of dry solids per day to be dewatered.
- Wet cake density
- The density of the filter cake varies from application to application and is used to accurately calculate the volume of filter cake generated. The density of the filter cake is also used to advise if extra support is needed in the structure of the filter press.
- Temperature of slurry
- The temperature of the slurry is used to select the appropriate materials of construction of the filter press as well as to determine its operating parameters.
Langley Separation and Process offers two options and/or both to help you determine the right filter press for your application or optimize your current filter press:
- On site pilot unit testing
- Sample lab testing

Full Circle Water Pilot units are essential for testing your process and proving out your specific dewatering or filtering application. On site pilot unit testing provides the opportunity to test a variety of conditions, configurations, and operating parameters. Langley Separation & Process can assist with setting up and running the pilot equipment to determine the optimal filter press configuration and operating conditions such as:
- Confirming sizing requirements
- Assisting with filter cloth selection
- Assisting with operating parameter optimization
- Selecting the correct filter plate for your process
- Identifying parameters for custom controls and process engineering support
- Provide commissioning and start up and/or ongoing maintenance support
- Generation of cake and filtrate for further testing or downstream process optimization
Langley Separation & Process can arrange for a rental pilot press. These pilot presses are available in a variety of sizes come complete with press, filter cloths and a feed pump. All you need to do is add an air supply, connect your feed tank, and start testing.
Available Rental and Pilot Unit Filter Presses:

250 mm
- filter press with up to 225-psig feed
470 mm
- Various cake thicknesses on non-gasketed plates
- Optional diaphragm squeeze plates (up to 225-psig)
- Up to 225-psig feed
- Press volume ranges from 0.3 to 2.0 ft3
630 mm
- 32-mm gasketed plates with (2) two cloth options
- Up to 100-psig feed
- Available at 4-ft3 or 8-ft3
800 mm
- 32 mm gasketed plates with (2) two options
- Up to 100-psig feed
- Press volume of 10-ft3
- Press volume of 20-ft3 – semi-automatic plate shifter is available
Langley Separation & Process can also assist with optimizing your current unit, planning a production change, or working through a filter press problem. If you are experiencing issues with filter cake or filtrate quality, making the changes necessary to investigate the problem can be difficult if you cannot take your filter press offline. Therefore, if you want to test different treatment chemistries, filter cloths, or make changes to cycle parameters then renting a pilot unit makes perfect sense. They operate offline so there is no impact on production.
Langley Separation & Process working with a world-class service network and technical resources that will keep your project moving and help you make the transition from pilot solution to fully equipped process system. And once your evaluation is complete, scaling up to a new filter press system is simple and virtually hassle-free because pilot presses are nearly identical to production systems.
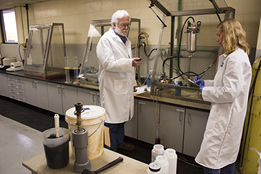
Langley Separation & Process can assist with submitting customer samples for in-house lab for testing. The fully staffed, state-of-the-art laboratory will determine the most effective liquid/solids separation techniques for each specific application and the most effective sludge conditioning, feed pressures, fill times, filter media, and filter cloths and press size for each customer.
In addition to ensuring a better-informed equipment selection and purchase, this customer-focused service will also help you maintain maximum performance of your filter press.
Laboratory Testing Analysis includes:
- Slurry or sludge characterization
- Filtration tests
- Characterization of filter cake
- Cloth evaluation
- J-Mate Continuous Dryer feasibility testing
Please contact Langley Separation & Process to schedule application consulting and lab services.
Langley Separation & Process also services a complete range of Filter Presses including Evoqua, JWI, J-PRESS®, US Filter, Perrin, Siemens as well as other brands of filter presses and can customize cost-effective preventive maintenance and support programs for your specific equipment, application, and / or facility requirement.
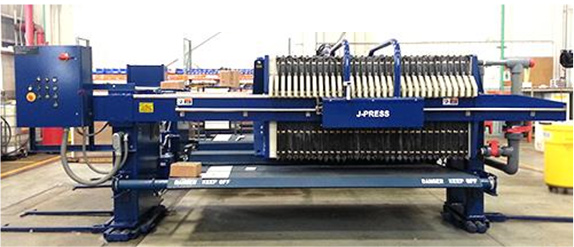
The J-Press filter press was the first to feature a single design that included:
- Self-compensating air/hydraulic closure system for ease of maintenance
- Gasketed filter plates for virtually leak free dewatering
- Semi-automatic plate shifting for labor savings and safety
- Automatic pump controls
- A paint coating that provided the highest level of protection from corrosion
The J-Press filter press quickly set the benchmark for filter press performance and today the Evoqua JWI J-Press filter press offers the most advanced automation available, from fully automatic plate shifting and cloth washing to PLC controls plus a full complement of ancillary slurry processing and cake handling system components. Adaptability to applications, processes and capacities are the underlying values of the JWI J-Press filter press.

Considered by industry professionals as the premier filter press, the J-Press filter press combines rugged construction, precision engineering, ease of operation plus a wide range of features and options to tackle the most difficult dewatering problems. These automated J-Press filter presses are key systems in municipal and industrial facilities around the world.
JWI J-Press filter press features include:
- Full range of capacities: 250-mm to 1000-mm
- Low and high pressure: 100-psi (7-bar), 225-psi (16-bar), higher pressure available — contact us
- Standard plate packs: Non-Gasketed Plates, Gasketed Plates, Diaphragm Squeeze Plates, Plate and Frame Stainless Steel Sidebar Covers
- Closure Systems: Manual, Automatic Closure (Air/ Hydraulic), Automatic Closure (Electric/Hydraulic)
- Control Systems: Standard Control Panel, Automatic Pump Control System, PLC
- Control Standard Manifolds: Air Blow Down Manifold, Double End Feed Manifold, Core Blow Down Manifold, Cake Wash Manifold, Precoat Manifold (other configurations available — contact us)
- Expansion options available for future capacity Plate Shifting: Air Operated Semi-Auto Plate Shifter, Automatic Pry Shifter, Automatic Pry Shifter and Bump, Automatic Pry Shifter, Bump and Weigh (ACDDS), Multi-Plate Pull
- Automatic Cloth Washing
- Material handling: Filter Cake Dumpster, Extended Legs and Chute, Platform, Drum Disposal System, Platform, Roll-off Container System Cake Conveyors
- Drip Trays: Manual, Automatic Spread Leg Design Safety: Splash Curtain, Safety Guard, Safety Light Curtains, Deadman Control Button, Safety Tripwire, Hyd. Clamp Pressure/Feed Pump, Interlock, Hyd. Control System/Press, Pressure Interlock, Hyd. Clamp Pressure/Squeeze, System Interlock
- Custom paint systems and coatings: Nicklad® Coating

The J-Press high performance filter press is available in three different frame designs with plate sizes ranging from 1.2 m x 1.2 m to 2.4 m x 2.4 m. The Sidebar filter press, the Overhead Compression Close filter press and the Overhead Tension Close filter press each offer fully automatic operation. Their unique construction and features make these large presses the best solution when balancing the requirements of the application with economies of the project.
Sidebar Compression Close:
A single hydraulic cylinder keeps the filter pack closed while in the compression stroke. Filter plates are suspended by the plate handles resting on the sidebar.
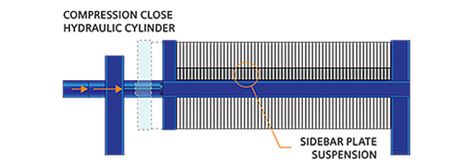
Advantages of Sidebar Compression Close:
- Available in a wider range of sizes, from 470-mm to 2.4-m x 2.4-m designs, with working pressure ratings of 100-psi (7-bar) and 225-psi (16-bar)
- Lighter weight than overhead designs
- Plates are easily accessible and removable from top
- Full range of automation options
- Available with air hydraulic systems in smaller sizes
- Less expensive than overhead designs

The Small Capacity J-Press Filter Press is the cost-effective solution for producing high solids filter cake with extremely high clarity in the liquid effluent. Considered by industry professionals as the premier sidebar filter press, the J-Press filter press combines rugged construction, precision engineering, ease of operation and a wide range of features and options to tackle the most difficult dewatering problems. The J-Press filter press is one of the most versatile dewatering devices on the market, being used in a wide variety of industrial and municipal applications. The J-Press filter press can be used to recover both solids and liquids from a waste or process stream. With superior materials of construction, the J-Press filter press is especially useful in the dewatering of aggressive acid and alkali suspensions.
The Small Capacity J-Press® Sidebar Filter Press can be fully automated to produce high solids filter cake with extremely high clarity in the liquid effluent. Available in a wide range of sizes and styles, the Small Capacity J-Press Filter Press can be configured to provide a dewatering solution to most all process flows from as little as 25 gallons to 1,000,000 gallons per day. It produces consistent results under varying influent conditions.

J-Press Larger Sidebar Filter Presses feature a heavy-duty carbon steel frame engineered to provide maximum rigidity for clamping forces exceeding 800,000-lbs. The J-Press side bar is available with 100-psi (7-bar), 225-psi (6-bar) or higher pressure configurations, with plate size and respective hydraulic capacities ranging from 1-m to 2-m x 2-m. The Large Capacity J-Press® Sidebar Filter Press robust features are engineered for long-term dewatering performance under the most demanding industrial municipal applications; a full complement of feed pumps, plate shifters, manifolds, and controls ensures efficient operation with minimal operator requirements. In addition, options for pretreatment, automatic cake release, cloth washing, material handling and safety features can be incorporated into a J-Press dewatering solution.
Sidebar Compression Close Unit Features and Benefits:
- Available in (4) four frame sizes from 1200-mm to 2000-mm made of heavy duty carbon steel plate and sheet, sandblasted and finished for maximum service life
- In order to optimize application performance the J-Press is available in 2 standard operating pressures of 100-psig (7-bar) and 225-psig (16-bar)and cake holding capacities from 50 (1.42 m3) to 600-ft3 (16.99 m3) -Self compensating electric/hydraulic closure system is standard to minimize labor requirements
- All process connections come pre-piped for plug-and-play installation (dependent on size, options selected and shipping restrictions)
- All filter plate wetted parts are polypropylene with PVC, carbon steel or stainless steel piping manifold for maximum corrosion resistance
Overhead Compression Close:
A single hydraulic cylinder keeps the filter pack closed while in the compression stroke. Filter plates are suspended by hangers from the overhead beam flange.

Advantages of Overhead Compression Close:
- Slightly smaller footprint than tension close
- More robust, heavy-duty frame construction than sidebar machines, accepts more chambers
- Overhead plate shifting minimizes cake contamination of shifter components
- Hydraulic cylinder mount and fixed head connected at four points for a more rigid base frame construction than sidebar machines
- Single overhead shifter mechanism reduces complexity of design
- No side rail interference allows full accessibility to the filter plates
Overhead Tension Close:
Hydraulic cylinders on all four corners keep the filter pack closed while in the tension stroke. Filter plates are suspended by hangers from the overhead beam flange.
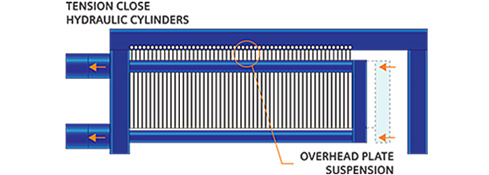
Advantages of Overhead Tension Close:
- Four hydraulic closing cylinders, positioned at the corners, give even distribution of closing load over sealing surfaces
- Each filter press offers only static loading to foundations (no dynamic load as with compression close machines) thereby making building design or steelwork simpler and less expensive
- Because the closing load is balanced between the four hydraulic cylinders these presses can be used with maximum number of chambers
- Evoqua is one of a limited number of experienced manufacturers for this style of filter press
J-Press® Overhead Filter Presses incorporate proven technologies in compression and tension designs and are the workhorse of high volume dewatering. Both bear the J-Press hallmark of exceptional performance under the most demanding applications, ease of use and minimal maintenance. In short, J-Press is engineered to deliver your greatest return on investment.
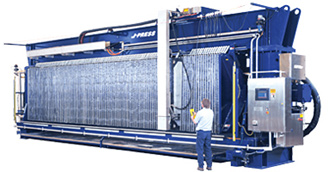
J-Press delivers high cake solids and clear filtrate, even with difficult alum sludge in municipal water production. Its solid, heavy steel construction is enhanced by intelligent design that permits easy access to all plates and operating parts. Available in a wide range of capacities and with feed pressures up to 20-bar, J-Press may be configured to your specifications for press filling, plate technology, dewatering, cake discharge, automation and takeaway. J-Press can adapt to different dewatering requirements, often with minimal change over, making it ideal for the flexibility often required in industrial processing. Available with comprehensive options, J-Press is designed to accommodate future expansions and continuous system improvements.
Overhead Tension Close Unit Feature & Benefits:
- Maintenance-free, corrosion-resistant rollers used on both plates and follower
- Variable speed shifter minimizes press cleaning time for more cycles per day
- Optional stainless steel wear strips on overhead beams at wheel contact points of suspension brackets assure long service life
- Easy access to filter plates — for manual or automatic cake removal, inspection and cloth servicing
- Plate suspension brackets designed to provide parallel plate movement and nesting without any swaying or skewing during shifting
- Plate shifter tightly nests plates and maintains consistent opening space from end to end
- Automatic latching mechanism ensures shifting of only one plate at a time
- Integrated circuits hydraulic technology provides exceptional press performance under a wide range of temperature, slurry and pressure requirements
- Air blowdown manifold aids in cake release while assuring maximum cake dryness and removal of residual filtrate
- Complete PLC capability for automatic sequencing of all press functions
- Adaptive Process Control results in consistently higher cake solids and shorter cycle times
Filter Press Parts and Service:
Langley Separation and Process can provide service and supply spare parts as well as an extensive selection of filter press cloths and filter press plates for Evoqua JWI, US Filter, Perrin, Siemens, Passavant, IPM and other brands of filter presses, plus parts for dryers including the JWI brand J-Mate® Dryer. We can even supply filter press accessories like cloth washers, drip tray, air blow, air hammers and much more.
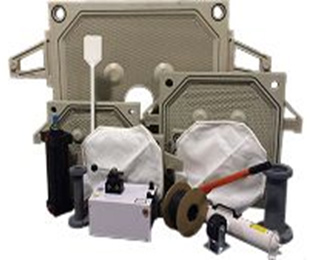
And if you are already an Evoqua customer Langley Separation and Process can help you with Evoqua’s new ToolDox® service portal. Evoqua’s secure ToolDOX®platform provides access to your dewatering equipment’s original OEM information by using the equipment’s unique serial number to view O&M manuals with exploded-view drawings including live parts look-up and built-in parts & service RFQs.
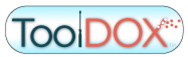
Langley Separation and Process can deliver individual filter presses and / or complete dewatering systems featuring custom automation / control panel, pumps, pipe work, feed / receiving tanks, polymer systems, mixers, skid packages, discharge augers, platforms and other accessories and options.
- Sludge thickening and storage tanks
- EQ tanks with vortex ring mixers
- Polymer and chemical addition systems
- Wastewater transfer and filter press feed pumps
- Filter cake transport conveyors
