Equipment Uptime Consulting
Whenever you need an outside perspective to evaluate and solve persistent equipment reliability or processing issues, or value-added expertise to help specify and manage an asset or complete project, our team of LS&P Up-time Specialist are ready to go to work for you.
Our Menu of Core Up-time Services Include:
- Specific Equipment Reliability Improvement Assignments
- (OEE) Overall Equipment / Process Effectiveness Evaluations
- Asset Care Maintenance and Reliability Programs
- Specific Asset Project Management
Our Menu of Core Equipment and Process Focus Includes:
- Decanter Centrifuges, Belt Presses, Screw Presses, Filter Presses and more
- Liquid / solids separation and solids / sludge dewatering processes
- Pretreatment mixing and feed equipment and preparation processes
- Post treatment solids / sludge drying equipment and processes
Specific Equipment Reliability Improvement Assignments
At Langley Separation & Process we focus our consultation services on liquid / solids separation and dewatering technologies and believe equipment uptime and reliability must be the aim of every plant operations program and viewed as an important success factor of the overall processing facility’s operating plan and a competitive advantage.
Our team of experienced, certified consultants bring years of unique “hands-on” experience over a wide cross section of dewatering equipment and process applications. We know your industry. When doing equipment and process consulting, we employ a systematic approach to increase asset utilization. Our Reliability Specialists Team will help you collect and analyze data on equipment downtime, onsite or remotely, and then analyze this data to identify both problems and opportunities in-order to improve uptime and overall equipment effectiveness.
Our proactive approach follows a prescribed process that we call, Your Path to Uptime.
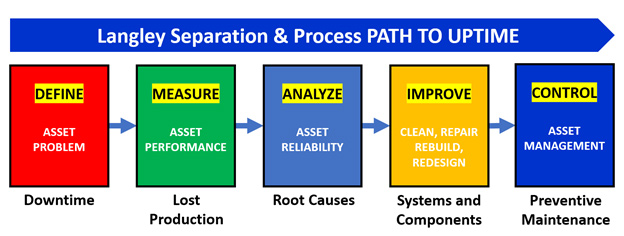
The key steps along this path are:
- Defining the scope of an asset issue in terms of its timing and location
- Measuring asset performance in terms of their impact on plant operations
- Analyzing the frequency of asset failures and understanding their effects root causes
- Assessing asset components to identify those requiring refurbishment or replacement
- Providing guidance on how to improve and maintain equipment and process to sustain performance
(OEE) Overall Equipment / Process Effectiveness Evaluations
The Langley Separation & Process Consulting Team understands that maximizing our client’s process throughput and equipment asset utilization is the key to reducing costs and increasing earnings. Our team begins the OEE process by obtaining and analyzing production data for downtime, scrap, rework, and output accounting for the various subcomponents of manufacturing (availability, utilization rate, and quality). Armed with this OEE information we can pinpoint the critical processes and assets (bad actors) and the underlying issues and root causes that must be addressed and improved to resolve production inefficiencies. Once these opportunities for improvement are identified the Langley Separation & Process Consulting Team will prepare specific roadmaps for improvement with timelines and budgets. This enables a client to evaluate the cost of our services against the obtainable outcomes.
Our mission is to make sure that by improving your overall equipment / process efficiencies in combination with maximizing the effectiveness of your equipment asset maintenance and management processes they become a competitive and sustainable long-term advantage that drive the (4) four benefits outlined below:
- Increasing operational plant availability to maximize your production
- Increasing production throughput to grow your operating profits
- Developing preventive and predictive maintenance strategies that increase equipment reliability and up-time
- Increasing your production unit margins by decreasing overall maintenance costs
Asset Care Maintenance and Reliability Programs
The Langley Separation & Process consulting team recognizes all production facilities require equipment and processes for manufacturing their products. We focus on providing an assessment of critical equipment assets to identify the assets and components required to bring equipment back to original OEM performance levels. We then conduct a diagnostic analysis of the maintenance management system to determine whether that function has the tools and information necessary to maintain said equipment asset at OEM performance levels. The objective of performing better maintenance is to improve equipment or process reliability and ensure that these assets are available to cost-effectively perform their required functions and produce quality products as scheduled.
Asset or process system performance is ultimately based on three (3) factors:
- Inherent Reliability | How it was designed?
- Operating Environment | How it will be operated?
- Maintenance Plan | How it will be maintained?
1) The Inherent Reliability of an asset refers to the level of reliability based on the configuration and specific use of equipment, processes, or individual components. Equipment and processes are typically designed with a certain level of Inherent Reliability. If certain assets or specific components are identified as having inherent reliability issues, The Langley Separation & Process Consulting Team has the expertise and resources available to help analyze these asset reliability issues or component part failures and provide a more reliable or cost-effective solution.
2) A second factor is evaluating the Operating Environment of the asset. This considers a variety of physical operating conditions under which the equipment and or process must operate. The skill level and training of the operators must also be considered as an environmental factor given operators are often the ones monitoring asset performance and initiating timely corrective actions upon recognizing any abnormal conditions. The Langley Separation & Process Consulting Team works with organizations to develop programs that ensure operators are appropriately educated and trained on the assets they work with to minimize operational equipment or process errors and failures.
3) The third factor is developing a comprehensive maintenance plan that defines how the asset will be maintained. The objective of a good maintenance plan is to maintain asset reliability and improve its up-time availability. The plan should include the necessary maintenance and service-type actions needed to detect potential failures before they lead to larger and more costly unscheduled downtime.
Langley Separation & Process Consulting Team’s Equipment Asset Care program’s focuses on helping companies establish and follow industrial practices that deliver on (3) three following major benefits:
- Improved Up Time
- Reduced Process Costs and Inefficiencies
- Increased Output / Capacity
Equipment Asset Component Part Solutions / Reverse Engineering
When tasked with an asset reliability improvement assignment the Langley Separation & Process Consulting Team analyzes the physical state and operating capability of assets to be improved. Typically, equipment assets fail because component parts fail. The solution is simple.
Prevent component part failure and equipment assets become more reliable.
All equipment asset reliability assignments begin by examining the required maintenance routines and the assets entire bill-of-materials to identify the most at-risk component parts. We then identify what can be done to minimize the risk by either improving the operating conditions or modifying the parts or equipment asset through reverse engineering to increase equipment asset reliability.
The Langley Separation & Process Consulting Team will update the company’s engineering, procurement, operating and maintenance program documentation once a solution has been identified, tested, and proven.
The Langley Separation & Process Consulting Team specializes in reverse engineering and modification of OEM parts. In many cases a re-engineered part can perform better and cost less to manufacture than the original. We use the latest in coordinate measuring technology, high quality measurements are taken from sample parts to produce a fully dimensioned model with all fits and tolerances and will also perform an in-depth material analysis. We carefully consider all options in determining materials and methods required to provide high quality reproductions that will be equal to the OEM part for fit and function at lowest possible costs.
In some instances, older equipment that is still operationally functional and appropriate for the application or business may no longer supported by the OEM or the original manufacture is no longer in business. This can make replacing old worn out or broken parts very expensive or impossible. In such cases reverse engineering replacement parts can be more practical and cost effective than completely replacing the equipment asset with new. In either case, except for OEM prices, the Langley Separation & Process Consulting Team will replicate parts that are indistinguishable from the OEM parts. Send us a sample for evaluation.
Does any of this sound familiar?
Constant unscheduled equipment and / or process downtime
Schedule delays and re-engineering resulting from inadequate communication with equipment suppliers, vendors and / or procurement?
Constant engineering and / or re-work due to lack of scope and charter at beginning of a project?
Inconsistent project designs impacting costs, scheduling, and safety?
Inefficient change order processes without applicable management visibility and scheduling updates?
Project engineers losing available time due to making changes and improvements as the scope is being developed on the fly?
Lack of project closeout documentation which affects future maintenance of equipment assets?
No critical reviews or formal assessments at project end which could facilitate future modifications and improvements?
Specific Asset Project Management
The Langley Separation & Process Consulting Team can assist with minor and even major capital equipment assets projects. Our project management approach includes proactive communication with all the capital equipment asset suppliers, engineering groups, component vendors, contractors and skilled trades and tapping into their expertise to understand and gather all the required information. Lack of proper communication, appropriate document control and adequate upfront planning typically plague many capital equipment asset projects resulting in poor equipment integration, costly budget, and schedule overruns.
Langley Separation & Process works to avoid these issues by clearly defining the necessary equipment assets, process designs, related components, purchasing requirements and task completion schedules. Once everything is identified and documented we will prepare specific recommendations and plans of action, timelines, and budgets. By successfully implementing and managing these basic practices at the beginning of a capital equipment asset project we can collectively produce the desired outcome.
See our Equipment Up-Time Consulting FAQs page to learn more.